Introduction to Electroplated Nickel in PCB Manufacturing
Electroplated nickel is a crucial process in the manufacturing of printed circuit boards (PCBs). This process involves depositing a thin layer of nickel onto the surface of the PCB through an electrochemical process. The nickel layer serves various purposes, including improving the solderability, enhancing the corrosion resistance, and providing a barrier layer between the copper substrate and the subsequent surface finishes.
In this article, we will delve into the details of the electroplated nickel process for PCBs, covering its importance, the process itself, the advantages and disadvantages, and the various applications in the electronics industry.
The Importance of Electroplated Nickel in PCBs
Enhancing Solderability
One of the primary reasons for applying an electroplated nickel layer on PCBs is to improve the solderability of the surface. Nickel has excellent wetting properties, which means that molten solder can easily spread and adhere to the surface during the soldering process. This ensures a strong and reliable solder joint between the PCB and the electronic components.
Providing Corrosion Resistance
PCBs are often exposed to harsh environmental conditions, such as moisture, humidity, and corrosive chemicals. The electroplated nickel layer acts as a protective barrier, preventing the underlying copper from corroding and deteriorating over time. This enhances the durability and longevity of the PCB, ensuring reliable performance in various applications.
Acting as a Barrier Layer
In many cases, the electroplated nickel layer serves as a barrier between the copper substrate and the subsequent surface finishes, such as gold or tin. The nickel layer prevents the diffusion of copper atoms into the surface finish, which can lead to the formation of intermetallic compounds and compromised solder joint integrity. By acting as a barrier, the nickel layer maintains the quality and reliability of the surface finish.
The Electroplated Nickel Process
Cleaning and Preparation
Before the electroplating process can begin, the PCB surface must be thoroughly cleaned and prepared. This involves removing any contaminants, such as oils, dirt, or oxides, from the surface. The cleaning process typically includes a series of chemical baths, such as alkaline cleaners and acid dips, followed by thorough rinsing with deionized water.
Activation
After cleaning, the PCB surface is activated to ensure proper adhesion of the electroplated nickel layer. This is usually done by immersing the PCB in an activation solution, such as a palladium-based activator, which creates a thin catalytic layer on the surface. This layer promotes the nucleation and growth of the nickel deposit during the electroplating process.
Electroplating
The electroplating process takes place in an electrolytic cell containing a nickel-based electrolyte solution. The PCB is connected to the cathode (negative terminal), while a nickel anode is connected to the positive terminal. When an electric current is applied, nickel ions from the electrolyte solution are reduced and deposited onto the PCB surface, forming a uniform and adherent nickel layer.
The electroplating parameters, such as current density, temperature, and pH, are carefully controlled to ensure the desired thickness, uniformity, and mechanical properties of the nickel layer. Typical nickel thicknesses range from 1 to 5 microns, depending on the specific application requirements.
Post-Treatment
After the electroplating process, the PCB undergoes post-treatment steps to enhance the quality and performance of the nickel layer. This may include a heat treatment process to improve the hardness and wear resistance of the nickel deposit. Additionally, the PCB may be subjected to a passivation treatment, such as immersion in a chromate solution, to further enhance the corrosion resistance of the nickel layer.
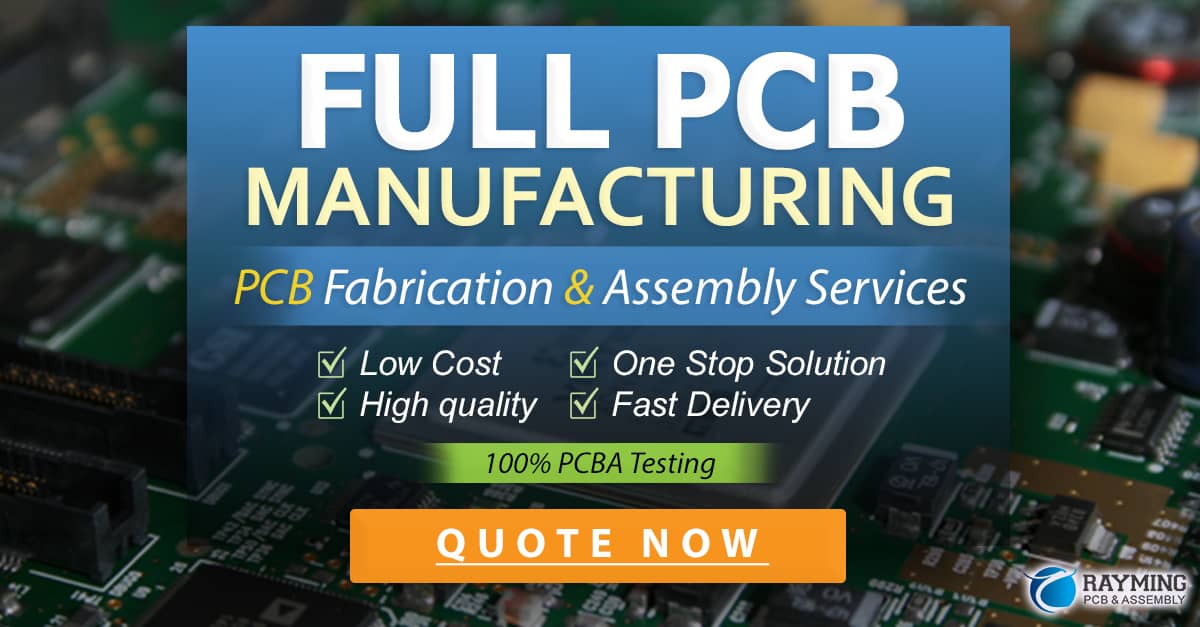
Advantages of Electroplated Nickel
-
Excellent solderability: The electroplated nickel layer provides excellent wetting properties, ensuring strong and reliable solder joints.
-
Enhanced corrosion resistance: Nickel acts as a protective barrier, preventing the underlying copper from corrosion and extending the lifespan of the PCB.
-
Barrier layer functionality: The nickel layer prevents the diffusion of copper into subsequent surface finishes, maintaining the integrity of the solder joint.
-
Improved wear resistance: Electroplated nickel provides good wear resistance, making it suitable for applications that involve mechanical stress or abrasion.
-
Compatibility with various surface finishes: Nickel is compatible with a wide range of surface finishes, such as gold, tin, and solder, making it a versatile choice for different applications.
Disadvantages of Electroplated Nickel
-
Cost: The electroplated nickel process adds an additional step to the PCB manufacturing process, which can increase the overall cost compared to other surface finishes.
-
Processing time: The electroplating process requires specific conditions and control, which can increase the processing time and affect the production throughput.
-
Environmental concerns: The electroplating process involves the use of chemicals and generates waste solutions that need to be properly treated and disposed of, raising environmental concerns.
-
Potential for hydrogen embrittlement: In some cases, the electroplated nickel layer may introduce hydrogen into the underlying copper, leading to hydrogen embrittlement and reduced mechanical strength.
Applications of Electroplated Nickel in PCBs
Automotive Electronics
Electroplated nickel is widely used in automotive electronics, such as engine control units, sensors, and infotainment systems. The enhanced corrosion resistance and durability provided by the nickel layer ensure reliable performance in the harsh automotive environment.
Industrial Control Systems
PCBs used in industrial control systems, such as programmable logic controllers (PLCs) and human-machine interfaces (HMIs), often rely on electroplated nickel for its corrosion resistance and solderability. These systems are exposed to harsh industrial environments, and the nickel layer helps maintain the integrity and reliability of the PCBs.
Aerospace and Defense
In aerospace and defense applications, PCBs are subjected to extreme conditions, including high temperatures, vibrations, and exposure to corrosive chemicals. Electroplated nickel is used to provide the necessary protection and ensure the reliable operation of critical electronic systems.
Medical Devices
Medical devices, such as implantable devices and diagnostic equipment, require high reliability and long-term stability. Electroplated nickel is used in these applications to provide corrosion resistance and ensure the integrity of the solder joints, contributing to the overall safety and effectiveness of the medical devices.
Future Trends in Electroplated Nickel for PCBs
As the electronics industry continues to evolve, there is a growing demand for advanced and reliable surface finishes for PCBs. Some of the future trends in electroplated nickel include:
-
Development of high-speed electroplating processes to improve production efficiency and reduce costs.
-
Exploration of alternative nickel alloys, such as nickel-phosphorus or nickel-cobalt, to enhance specific properties like hardness or wear resistance.
-
Adoption of environmentally friendly electroplating processes and chemistries to minimize the environmental impact and comply with strict regulations.
-
Integration of electroplated nickel with other surface finishes, such as palladium or silver, to achieve unique combinations of properties for specific applications.
Frequently Asked Questions (FAQ)
1. What is the typical thickness of the electroplated nickel layer on PCBs?
The typical thickness of the electroplated nickel layer on PCBs ranges from 1 to 5 microns, depending on the specific application requirements and the desired properties.
2. Can electroplated nickel be used as a final surface finish on PCBs?
Yes, electroplated nickel can be used as a final surface finish on PCBs, providing good solderability and corrosion resistance. However, in many cases, it is used as a barrier layer between the copper substrate and other surface finishes like gold or tin.
3. How does electroplated nickel compare to other surface finishes in terms of cost?
Electroplated nickel is generally more expensive compared to other surface finishes like immersion tin or organic solderability preservatives (OSPs). However, it offers superior corrosion resistance and solderability, making it a cost-effective choice for applications that require high reliability and durability.
4. Is electroplated nickel suitable for high-frequency PCB applications?
Yes, electroplated nickel is suitable for high-frequency PCB applications. The nickel layer provides a smooth and uniform surface, which helps minimize signal loss and maintains the integrity of high-frequency signals.
5. Are there any environmental concerns associated with the electroplated nickel process?
Yes, the electroplated nickel process involves the use of chemicals and generates waste solutions that need to be properly treated and disposed of. PCB manufacturers must comply with environmental regulations and implement proper waste management practices to minimize the environmental impact of the process.
Conclusion
Electroplated nickel is a crucial process in the manufacturing of printed circuit boards, providing enhanced solderability, corrosion resistance, and barrier layer functionality. By understanding the importance, process, advantages, and applications of electroplated nickel, PCB designers and manufacturers can make informed decisions when selecting surface finishes for their products.
As the electronics industry continues to advance, it is essential to stay updated with the latest trends and developments in electroplated nickel technology. By adopting innovative processes, exploring alternative materials, and prioritizing environmental sustainability, the industry can ensure the continued success and reliability of PCBs in various applications.
Property | Electroplated Nickel |
---|---|
Typical Thickness | 1-5 microns |
Solderability | Excellent |
Corrosion Resistance | High |
Barrier Layer Function | Yes |
Wear Resistance | Good |
Compatibility with Surface Finishes | Wide Range |
Cost | Moderate to High |
Processing Time | Longer |
Environmental Concerns | Yes |
By leveraging the benefits of electroplated nickel and addressing the associated challenges, PCB manufacturers can deliver high-quality and reliable products that meet the ever-increasing demands of the electronics industry. As technology continues to evolve, the role of electroplated nickel in PCB manufacturing is expected to remain significant, driving innovation and enabling the development of advanced electronic systems across various sectors.
0 Comments