Introduction to BGA Solderability
Ball Grid Array (BGA) packages have become increasingly popular in electronics manufacturing due to their high density interconnects and compact size. Ensuring the solderability of BGA components is critical for achieving reliable solder joints and avoiding defects during the assembly process. This article delves into the BGA Solderability Standards, testing methods, acceptance criteria, and best practices for optimizing BGA solderability.
What is BGA Solderability?
BGA solderability refers to the ability of the BGA package’s solder balls to form reliable solder joints with the corresponding pads on the printed circuit board (PCB) during the reflow soldering process. Good BGA solderability is characterized by:
- Uniform and complete wetting of solder balls to the PCB pads
- Absence of defects such as voids, bridges, or non-wet solder balls
- Strong mechanical and electrical integrity of the solder joints
Poor BGA solderability can lead to various defects that compromise the reliability and functionality of the assembled product. Some common BGA solderability defects include:
- Non-wet or partially-wet solder balls
- Solder bridges between adjacent balls
- Voids within the solder joints
- Misaligned or missing solder balls
Factors Affecting BGA Solderability
Several factors can influence the solderability of BGA packages:
-
Surface finish of BGA balls: The surface finish of the BGA solder balls plays a crucial role in solderability. Common surface finishes include Sn-Pb, lead-free (SAC alloys), and Ni/Au. The choice of surface finish depends on the application requirements and compatibility with the solder paste used.
-
Storage conditions and shelf life: Improper storage conditions and prolonged shelf life can degrade the solderability of BGA packages. Exposure to moisture, high temperatures, or contamination can lead to oxidation or degradation of the solder ball surface.
-
Reflow profile: The reflow soldering profile, including peak temperature, time above liquidus (TAL), and cooling rate, can impact BGA solderability. An optimized reflow profile ensures proper wetting and minimizes defects.
-
Solder paste: The selection of solder paste, including alloy composition and powder particle size, should be compatible with the BGA package’s surface finish and the reflow profile used.
-
PCB design and surface finish: The PCB pad design, size, and surface finish also influence BGA solderability. Proper pad design and compatible surface finishes promote good wetting and reliable solder joints.
BGA Solderability Standards
Various industry standards provide guidelines and requirements for BGA solderability testing and acceptance criteria. Some of the key standards include:
IPC J-STD-002
IPC J-STD-002, “Solderability Tests for Component Leads, Terminations, Lugs, Terminals, and Wires,” is a widely used standard for assessing the solderability of electronic components, including BGA packages. It defines test methods, procedures, and acceptance criteria for solderability testing.
The standard specifies three main test methods for BGA solderability:
-
Dip and Look Test (D&L): In this test, the BGA package is dipped into a molten solder bath for a specified time and then visually inspected for wetting and defects.
-
Wetting Balance Test (WBT): This test measures the wetting force and time of the BGA solder balls when immersed in a molten solder bath. It provides quantitative data on the solderability performance.
-
Solder Ball Shear Test (SBST): The SBST evaluates the mechanical strength of individual solder balls by applying a shear force until failure. It assesses the integrity of the solder ball attachment to the package substrate.
IPC J-STD-002 also defines the acceptance criteria for BGA solderability based on the visual inspection and measurable parameters from the tests. Some key acceptance criteria include:
- Minimum percentage of solder ball coverage (wetting) after D&L test
- Maximum wetting time and minimum wetting force in WBT
- Minimum shear force and failure mode in SBST
IEC 60068-2-58
IEC 60068-2-58, “Environmental testing – Part 2-58: Tests – Test Td: Test methods for solderability, resistance to dissolution of metallization and to soldering heat of surface mounting devices (SMD),” is another international standard that covers solderability testing for surface mount devices, including BGAs.
This standard specifies similar test methods as IPC J-STD-002, such as the dip and look test and wetting balance test. It also provides guidance on sample preparation, test conditions, and acceptance criteria for BGA solderability.
JEDEC J-STD-020 and J-STD-033
JEDEC standards J-STD-020, “Moisture/Reflow Sensitivity Classification for Nonhermetic Surface Mount Devices,” and J-STD-033, “Handling, Packing, Shipping and Use of Moisture/Reflow Sensitive Surface Mount Devices,” are related to moisture sensitivity and handling of BGA packages, which can impact solderability.
J-STD-020 defines the moisture sensitivity levels (MSLs) for surface mount devices and provides the reflow profiles and conditions for testing moisture sensitivity. Proper handling and baking of moisture-sensitive BGAs according to their MSL is essential to maintain solderability.
J-STD-033 provides guidelines for the handling, packing, shipping, and use of moisture-sensitive devices, including BGAs. Following these guidelines helps prevent moisture-induced damage and maintains the solderability of the components.
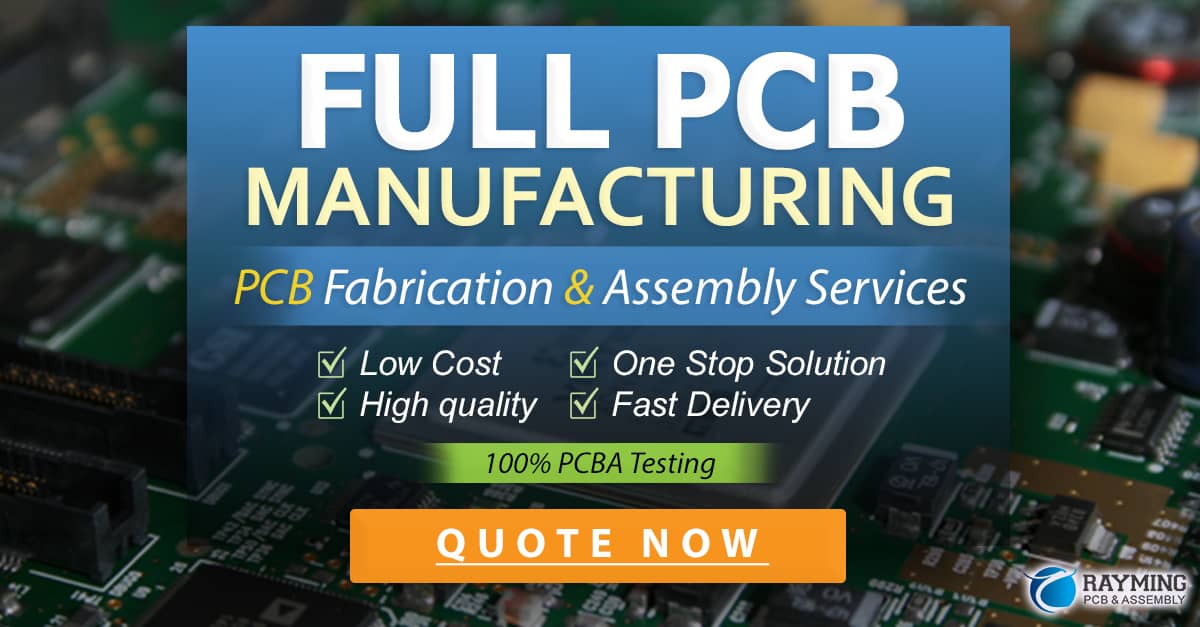
BGA Solderability Testing
Solderability testing is performed to assess the ability of BGA packages to form reliable solder joints during the assembly process. The following table summarizes the common BGA solderability test methods and their purposes:
Test Method | Purpose |
---|---|
Dip and Look Test (D&L) | Visual assessment of solder ball wetting and defects |
Wetting Balance Test (WBT) | Quantitative measurement of wetting force and time |
Solder Ball Shear Test (SBST) | Evaluation of solder ball mechanical strength |
Sample Preparation
Proper sample preparation is crucial for accurate and reliable solderability testing. The BGA packages should be handled and stored according to the manufacturer’s recommendations and the relevant JEDEC standards (J-STD-020 and J-STD-033) to prevent moisture absorption and degradation.
Before testing, the BGA packages should be visually inspected for any damage, contamination, or defects that could affect solderability. The packages should be cleaned, if necessary, using appropriate methods such as isopropyl alcohol or other cleaning agents recommended by the manufacturer.
Test Conditions
The test conditions for BGA solderability testing should be carefully controlled to ensure consistent and repeatable results. Some key test conditions include:
- Solder bath temperature and composition
- Dipping time and depth
- Wetting balance parameters (immersion depth, dwell time, withdrawal speed)
- Shear test parameters (shear height, shear speed, shear tool)
The specific test conditions are usually specified in the relevant standards (IPC J-STD-002 or IEC 60068-2-58) and should be followed accordingly.
Acceptance Criteria
The acceptance criteria for BGA solderability are based on the visual inspection and measurable parameters from the solderability tests. The following table provides an example of typical acceptance criteria for BGA solderability:
Test Method | Acceptance Criteria |
---|---|
D&L | Minimum 95% solder ball coverage (wetting) |
No bridging, non-wetting, or other defects | |
WBT | Maximum wetting time: 2 seconds |
Minimum wetting force: 0.1 mN/mm of solder ball diameter | |
SBST | Minimum shear force: 1.0 kgf per solder ball |
Ductile failure mode (no interfacial or brittle failures) |
The specific acceptance criteria may vary depending on the applicable standard, BGA package type, and customer requirements. It is essential to refer to the relevant specifications and agree upon the acceptance criteria with the stakeholders involved.
Best Practices for Optimizing BGA Solderability
To optimize BGA solderability and ensure reliable solder joints, consider the following best practices:
-
Storage and Handling: Store BGA packages in a controlled environment with proper moisture protection and ESD precautions. Follow the manufacturer’s recommendations and JEDEC standards for storage conditions and shelf life.
-
Moisture Management: Manage moisture-sensitive BGAs according to their MSL classification. Bake components before assembly if exposed to excessive moisture or if the floor life has been exceeded.
-
Solder Paste Selection: Choose a compatible solder paste with the appropriate alloy composition and powder particle size for the BGA package and PCB surface finishes.
-
Stencil Design: Use a stencil with the appropriate aperture size and shape for the BGA solder balls. Consider solder paste volume and area ratio for optimal solder joint formation.
-
Reflow Profile Optimization: Develop and optimize the reflow soldering profile based on the BGA package, solder paste, and PCB characteristics. Ensure proper peak temperature, TAL, and cooling rate to achieve good wetting and minimize defects.
-
Inspection and Quality Control: Implement a robust inspection and quality control process to verify BGA solderability and solder joint integrity. Use visual inspection, X-ray, or automated optical inspection (AOI) methods to detect and analyze defects.
-
Process Validation: Validate the BGA assembly process through solderability testing, cross-sectioning, and reliability assessments. Continuously monitor and control the process parameters to maintain consistent solderability.
-
Training and Certification: Provide appropriate training and certification to personnel involved in BGA assembly and solderability testing. Ensure they are knowledgeable about the standards, procedures, and best practices.
Frequently Asked Questions (FAQ)
-
What is BGA solderability, and why is it important?
BGA solderability refers to the ability of the BGA package’s solder balls to form reliable solder joints with the PCB pads during the reflow soldering process. It is important because poor solderability can lead to defects, reduced reliability, and potential failures in the assembled product. -
What are the main factors that affect BGA solderability?
The main factors affecting BGA solderability include the surface finish of the BGA balls, storage conditions and shelf life, reflow profile, solder paste selection, and PCB design and surface finish. -
What are the common BGA solderability test methods?
The common BGA solderability test methods are the Dip and Look (D&L) test, Wetting Balance Test (WBT), and Solder Ball Shear Test (SBST). These tests assess the wetting, wetting force and time, and mechanical strength of the solder balls, respectively. -
How can I optimize BGA solderability in my assembly process?
To optimize BGA solderability, follow best practices such as proper storage and handling, moisture management, compatible solder paste selection, optimized stencil design, reflow profile optimization, thorough inspection and quality control, process validation, and personnel training and certification. -
What are the acceptance criteria for BGA solderability?
The acceptance criteria for BGA solderability vary depending on the applicable standards and specific requirements. Generally, they include minimum solder ball coverage (wetting) percentage, maximum wetting time, minimum wetting force, minimum shear force, and acceptable failure modes. Refer to the relevant standards and specifications for the exact criteria.
Conclusion
BGA solderability is a critical aspect of electronics manufacturing that directly impacts the reliability and quality of the assembled products. Understanding the BGA solderability standards, testing methods, acceptance criteria, and best practices is essential for ensuring robust and defect-free solder joints.
By following the guidelines outlined in industry standards such as IPC J-STD-002, IEC 60068-2-58, and JEDEC J-STD-020 and J-STD-033, manufacturers can effectively assess and optimize BGA solderability. Implementing appropriate storage and handling procedures, selecting compatible materials, optimizing the assembly process, and conducting thorough inspections and validations are key to achieving consistent and reliable BGA solderability.
As technology advances and miniaturization continues, the importance of BGA solderability will only increase. Staying updated with the latest standards, best practices, and technological developments is crucial for manufacturers to meet the evolving demands of the electronics industry and deliver high-quality, reliable products to their customers.
0 Comments