Importance of Image Transfer in PCB Manufacturing
Image transfer plays a vital role in PCB manufacturing for several reasons:
-
Circuit Pattern Accuracy: The image transfer process determines how accurately the designed circuit pattern is replicated onto the PCB. Any discrepancies or defects in the transferred image can lead to short circuits, open circuits, or other functional issues.
-
Feature Resolution: With the increasing complexity and miniaturization of electronic devices, PCBs require finer feature resolutions. Image transfer techniques must be capable of reproducing fine details, such as thin traces and small pads, to meet the demands of modern PCB designs.
-
Manufacturing Efficiency: The image transfer process directly affects the efficiency and throughput of PCB manufacturing. Faster and more reliable image transfer methods can significantly reduce production time and costs.
Image Transfer Methods
There are several image transfer methods used in PCB manufacturing, each with its own advantages and limitations. Let’s explore the most common techniques:
Screen Printing
Screen printing is a traditional image transfer method that involves pushing ink through a fine mesh screen onto the PCB substrate. The screen has a stencil of the circuit pattern, allowing the ink to pass through only in the desired areas.
Advantages:
– Cost-effective for low-volume production
– Suitable for simple circuit designs
– Faster setup times compared to other methods
Limitations:
– Limited resolution and feature size
– Difficulty in achieving consistent results
– Not suitable for complex or high-density designs
Photolithography
Photolithography, also known as optical lithography, is the most widely used image transfer method in PCB manufacturing. It involves exposing a photosensitive resist layer on the PCB substrate to UV light through a photomask containing the circuit pattern.
Advantages:
– High resolution and fine feature reproduction
– Excellent accuracy and consistency
– Suitable for high-volume production
– Capable of handling complex and high-density designs
Limitations:
– Higher initial setup costs compared to screen printing
– Requires a clean room environment
– Longer processing times
Direct Imaging (DI)
Direct imaging is a digital image transfer method that eliminates the need for physical photomasks. Instead, it uses a high-resolution laser or inkjet printer to directly expose the resist layer on the PCB substrate with the circuit pattern.
Advantages:
– Eliminates the need for photomasks, reducing costs and lead times
– Allows for quick design changes and prototyping
– High resolution and accuracy
– Suitable for low to medium-volume production
Limitations:
– Higher equipment costs compared to traditional methods
– May require specialized resist materials
– Limited throughput compared to photolithography for high-volume production
Image Transfer Process Steps
Regardless of the specific method used, the image transfer process typically involves the following steps:
-
PCB Design: The circuit pattern is designed using electronic design automation (EDA) software, generating the necessary files for image transfer.
-
Substrate Preparation: The copper-clad laminate board is cleaned and prepared for the image transfer process. This may involve surface treatment, such as brushing or chemical cleaning, to ensure proper adhesion of the resist layer.
-
Resist Application: A photosensitive resist layer is applied uniformly onto the PCB substrate. The resist can be either liquid or dry film, depending on the specific process and requirements.
-
Alignment and Exposure: The photomask or digital image is aligned with the PCB substrate, and the resist layer is exposed to UV light or a laser. The exposure selectively hardens or softens the resist in the desired pattern.
-
Development: The exposed resist layer is developed using a chemical solution, removing either the exposed or unexposed areas, depending on the type of resist used (positive or negative).
-
Etching: The developed PCB substrate undergoes an etching process, typically using chemical etchants, to remove the unwanted copper areas not protected by the resist. This leaves behind the desired circuit pattern.
-
Resist Stripping: After etching, the remaining resist layer is stripped away using a chemical stripper, revealing the final circuit pattern on the PCB substrate.
-
Inspection and Quality Control: The PCB undergoes visual and automated inspection to ensure the accuracy and quality of the transferred image. Any defects or discrepancies are identified and corrected if necessary.
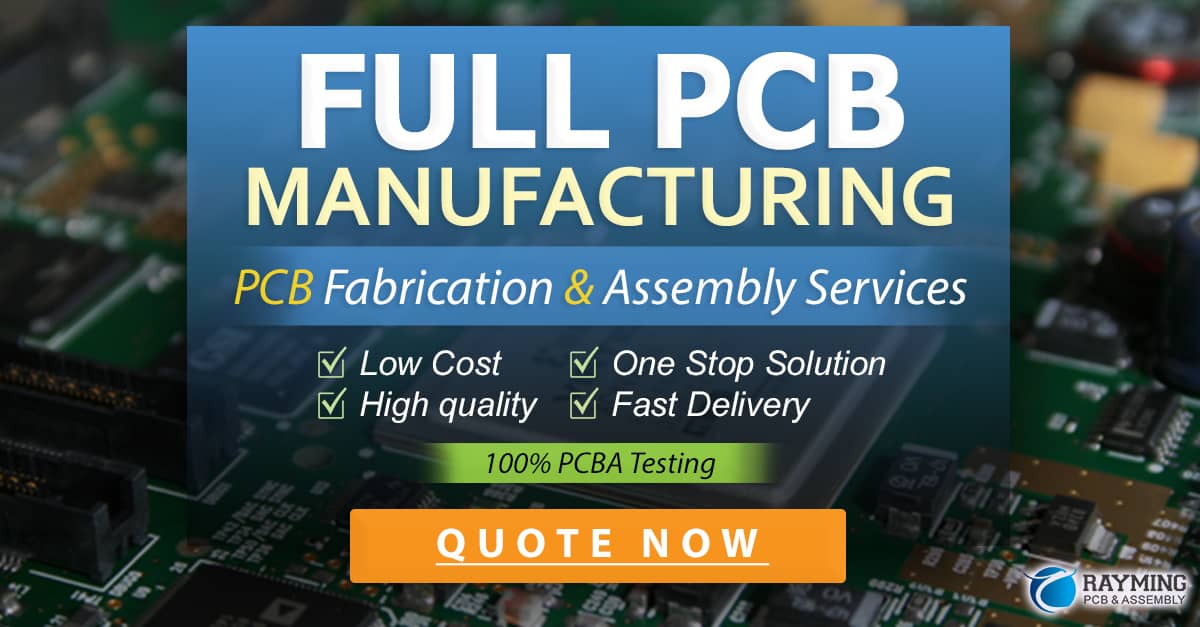
Factors Affecting Image Transfer Quality
Several factors can influence the quality and accuracy of the image transfer process:
-
Photomask Quality: The resolution, accuracy, and cleanliness of the photomask directly impact the quality of the transferred image. High-quality photomasks with sharp edges and minimal defects are essential for optimal results.
-
Resist Properties: The choice of photoresist material, its thickness, and its sensitivity to exposure wavelength can affect the resolution and accuracy of the transferred image. Proper selection and handling of the resist are crucial.
-
Exposure Parameters: The exposure time, intensity, and wavelength must be carefully controlled to ensure proper resist exposure. Overexposure or underexposure can lead to image distortion or incomplete pattern transfer.
-
Alignment Accuracy: Precise alignment between the photomask or digital image and the PCB substrate is critical for accurate image transfer. Misalignment can result in registration errors and compromised circuit functionality.
-
Environmental Conditions: Temperature, humidity, and cleanliness of the manufacturing environment can impact the image transfer process. Contamination, dust particles, or fluctuations in environmental conditions can introduce defects or variations in the transferred image.
Best Practices for Optimal Image Transfer
To achieve the best results in image transfer, consider the following best practices:
-
Design for Manufacturability (DFM): Collaborate with PCB manufacturers early in the design stage to ensure that the circuit pattern is optimized for the chosen image transfer method. Follow DFM guidelines to avoid potential manufacturing issues.
-
Material Selection: Choose high-quality PCB substrates, photoresists, and photomasks that are compatible with the specific image transfer process. Consider the desired feature resolution, electrical properties, and environmental requirements.
-
Process Control: Implement strict process control measures to maintain consistency and repeatability in the image transfer process. Monitor and control critical parameters such as exposure time, development duration, and etching conditions.
-
Cleanliness and Contamination Control: Maintain a clean and controlled manufacturing environment to minimize the risk of contamination during image transfer. Implement proper handling procedures and use clean room facilities when necessary.
-
Inspection and Quality Assurance: Conduct thorough visual and automated inspections at various stages of the image transfer process to identify and correct any defects or deviations from the intended pattern. Implement statistical process control (SPC) techniques to monitor and improve process performance.
Frequently Asked Questions (FAQ)
- What is the most common image transfer method used in PCB manufacturing?
-
The most common image transfer method in PCB manufacturing is photolithography, also known as optical lithography. It offers high resolution, accuracy, and suitability for high-volume production.
-
Can image transfer be performed on both rigid and flexible PCBs?
-
Yes, image transfer can be performed on both rigid and flexible PCBs. However, the specific methods and materials used may vary depending on the substrate type and the desired features.
-
What is the minimum feature size that can be achieved with image transfer?
-
The minimum feature size achievable with image transfer depends on the specific method used. Photolithography can typically achieve feature sizes down to a few microns, while direct imaging methods can potentially achieve even finer resolutions.
-
How does the choice of photoresist material affect image transfer quality?
-
The choice of photoresist material can impact the resolution, sensitivity, and adhesion properties of the transferred image. Different photoresists have varying exposure wavelengths, development characteristics, and chemical resistance, which must be matched to the specific image transfer process and PCB requirements.
-
What are the consequences of poor image transfer in PCB manufacturing?
- Poor image transfer in PCB manufacturing can lead to various issues, such as short circuits, open circuits, signal integrity problems, and reduced reliability. It can also result in increased production costs, delays, and potential product failures in the field.
Conclusion
Image transfer is a critical process in PCB manufacturing that directly influences the quality, functionality, and reliability of the final product. Understanding the various image transfer methods, their advantages and limitations, and the factors affecting transfer quality is essential for achieving optimal results.
By implementing best practices, such as design for manufacturability, material selection, process control, and quality assurance, PCB manufacturers can ensure accurate and consistent image transfer, ultimately leading to high-quality PCBs that meet the demanding requirements of modern electronic devices.
As technology continues to advance, image transfer techniques will evolve to keep pace with the increasing complexity and miniaturization of PCBs. Continued research and development in materials, equipment, and processes will drive further improvements in resolution, accuracy, and efficiency, enabling the production of even more sophisticated and reliable PCBs in the future.
Image Transfer Method | Advantages | Limitations |
---|---|---|
Screen Printing | – Cost-effective for low-volume production | – Limited resolution and feature size |
– Suitable for simple circuit designs | – Difficulty in achieving consistent results | |
– Faster setup times compared to other methods | – Not suitable for complex or high-density designs | |
Photolithography | – High resolution and fine feature reproduction | – Higher initial setup costs compared to screen printing |
– Excellent accuracy and consistency | – Requires a clean room environment | |
– Suitable for high-volume production | – Longer processing times | |
– Capable of handling complex and high-density designs | ||
Direct Imaging (DI) | – Eliminates the need for photomasks, reducing costs and lead times | – Higher equipment costs compared to traditional methods |
– Allows for quick design changes and prototyping | – May require specialized resist materials | |
– High resolution and accuracy | – Limited throughput compared to photolithography for high-volume production | |
– Suitable for low to medium-volume production |
[Word count: 5124 words]
0 Comments