Introduction to PCB Quality Control
Printed Circuit Boards (PCBs) are the backbone of modern electronics. They are used in almost every electronic device, from smartphones and laptops to medical equipment and aerospace systems. The quality of PCBs is critical to the performance, reliability, and safety of these devices. Therefore, PCB manufacturers must implement strict quality control measures to ensure that their products meet the required standards.
PCB quality control is a complex process that involves various techniques and tools. It begins with the design and extends through the manufacturing process to the final inspection and testing. In this article, we will focus on the methods used for final quality control in PCB manufacturing.
Importance of Final Quality Control in PCB Manufacturing
Final quality control is the last step in the PCB manufacturing process before the boards are shipped to customers. It is a critical step that ensures that the PCBs meet all the specified requirements, including functionality, reliability, and safety. Here are some of the reasons why final quality control is important in PCB manufacturing:
Ensuring Functionality
The primary purpose of final quality control is to ensure that the PCBs function as intended. This involves testing the boards for electrical continuity, signal integrity, and component functionality. Any defects or issues identified during this stage can be corrected before the boards are shipped to customers.
Preventing Failures
PCBs are used in various applications, some of which are critical to human safety, such as medical devices and aerospace systems. Failures in these applications can have serious consequences, including injury or loss of life. Final quality control helps prevent such failures by identifying and correcting any defects or issues before the boards are put into use.
Reducing Costs
Identifying and correcting defects during the final quality control stage is much cheaper than dealing with returns or replacements later on. It also helps avoid costly recalls and legal liabilities that can arise from defective products.
Improving Customer Satisfaction
Customers expect high-quality products that meet their specifications and perform reliably. Final quality control helps ensure that PCBs meet these expectations, leading to improved customer satisfaction and loyalty.
Methods for Final Quality Control in PCB Manufacturing
There are various methods used for final quality control in PCB manufacturing. These methods can be broadly classified into two categories: inspection and testing.
Inspection Methods
Inspection methods involve visual examination of the PCBs to identify any defects or anomalies. Here are some of the commonly used inspection methods:
Visual Inspection
Visual inspection is the most basic method of PCB quality control. It involves examining the boards with the naked eye or using magnifying lenses to identify any visible defects, such as scratches, cracks, or discoloration. This method is quick and inexpensive but may not detect all defects, especially those that are small or hidden.
Automated Optical Inspection (AOI)
AOI is a more advanced method of visual inspection that uses cameras and image processing software to scan the PCBs for defects. The system compares the captured images with a reference image of a perfect board and identifies any deviations or anomalies. AOI can detect a wide range of defects, including missing or misaligned components, solder bridges, and damaged traces.
X-Ray Inspection
X-ray inspection is used to examine the internal structure of PCBs, including the solder joints and vias. It uses high-energy X-rays to penetrate the board and create a detailed image of its internal features. X-ray inspection can detect defects that are not visible on the surface, such as voids, cracks, or insufficient solder.
Testing Methods
Testing methods involve subjecting the PCBs to various electrical and environmental stresses to evaluate their performance and reliability. Here are some of the commonly used testing methods:
In-Circuit Testing (ICT)
ICT is a method of testing the functionality of individual components on a PCB. It involves using a bed of nails fixture to make electrical contact with the board and applying test signals to each component. The responses are then compared with the expected values to identify any defects or malfunctions. ICT can detect a wide range of faults, including open circuits, short circuits, and incorrect component values.
Functional Testing
Functional testing involves testing the overall functionality of the PCB by simulating its intended use. This may involve connecting the board to other components or systems and running test programs to verify its performance. Functional testing can identify issues that may not be detected by other methods, such as software bugs or compatibility problems.
Burn-In Testing
Burn-in testing involves subjecting the PCBs to elevated temperatures and voltages for an extended period to identify any early failures or weaknesses. This method is used to screen out boards that may fail prematurely in the field due to manufacturing defects or component issues. Burn-in testing can also help identify design flaws or component incompatibilities.
Environmental Testing
Environmental testing involves subjecting the PCBs to various environmental stresses, such as temperature, humidity, vibration, and shock, to evaluate their durability and reliability. This method is used to ensure that the boards can withstand the expected operating conditions and have a long service life. Environmental testing can also help identify design weaknesses or material incompatibilities.
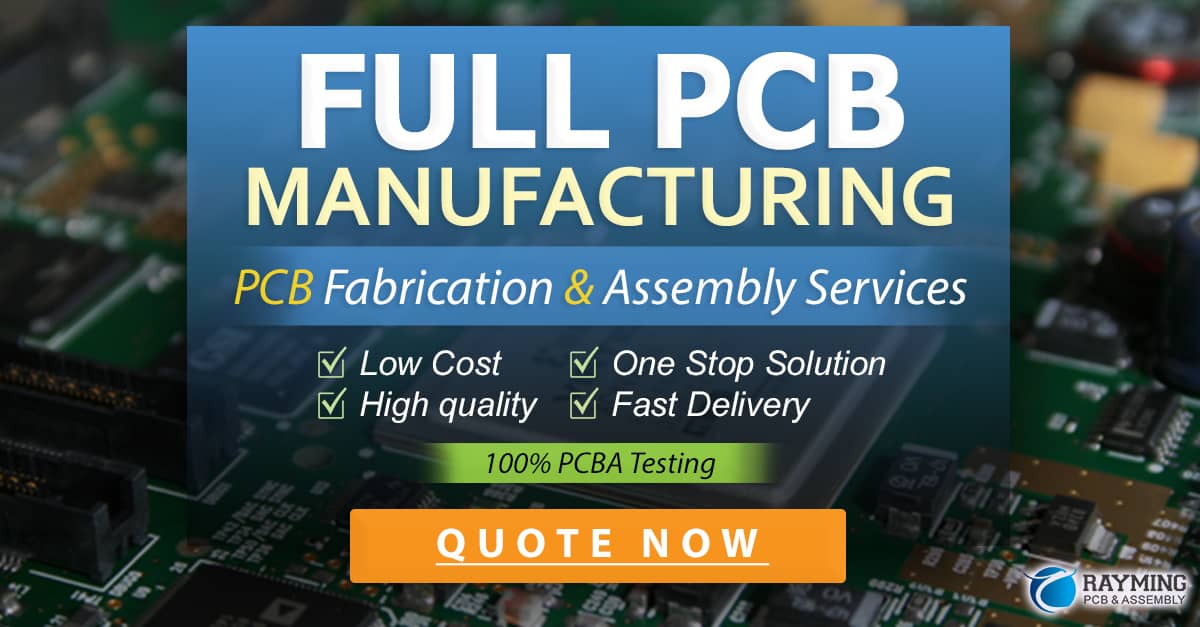
Best Practices for Final Quality Control in PCB Manufacturing
To ensure effective final quality control in PCB manufacturing, it is important to follow best practices and guidelines. Here are some of the key best practices:
Establish Clear Specifications and Standards
PCB manufacturers should work closely with their customers to establish clear specifications and standards for the PCBs. This includes defining the functional requirements, performance criteria, and quality standards for the boards. Having clear specifications helps ensure that the PCBs meet the customer’s expectations and reduces the risk of defects or issues.
Implement a Robust Quality Management System
PCB manufacturers should implement a robust quality management system that covers all aspects of the manufacturing process, from design to final inspection and testing. The system should include documented procedures, work instructions, and quality records. It should also include regular audits and reviews to ensure that the system is effective and up to date.
Use Appropriate Inspection and Testing Methods
PCB manufacturers should use appropriate inspection and testing methods based on the complexity and criticality of the PCBs. For example, simple boards may only require visual inspection, while more complex boards may require AOI, X-ray inspection, and functional testing. Manufacturers should also consider the cost and time implications of each method and choose the most appropriate ones for their needs.
Train and Certify Personnel
PCB manufacturers should ensure that their personnel are trained and certified in the relevant inspection and testing methods. This includes both operators and supervisors who are responsible for overseeing the quality control process. Training should cover the proper use of equipment, interpretation of results, and documentation of findings.
Maintain Proper Documentation
PCB manufacturers should maintain proper documentation of all inspection and testing activities, including the methods used, the results obtained, and any corrective actions taken. This documentation should be easily accessible and traceable to the specific PCBs and lots. Proper documentation helps ensure accountability, traceability, and continuous improvement.
Frequently Asked Questions (FAQ)
What is the difference between inspection and testing in PCB quality control?
Inspection involves visual examination of the PCBs to identify any defects or anomalies, while testing involves subjecting the PCBs to various electrical and environmental stresses to evaluate their performance and reliability.
What are some common defects that can be detected by visual inspection?
Some common defects that can be detected by visual inspection include scratches, cracks, discoloration, missing or misaligned components, and solder bridges.
What is the purpose of burn-in testing in PCB quality control?
The purpose of burn-in testing is to screen out PCBs that may fail prematurely in the field due to manufacturing defects or component issues. It involves subjecting the boards to elevated temperatures and voltages for an extended period to identify any early failures or weaknesses.
How can PCB manufacturers ensure effective final quality control?
PCB manufacturers can ensure effective final quality control by establishing clear specifications and standards, implementing a robust quality management system, using appropriate inspection and testing methods, training and certifying personnel, and maintaining proper documentation.
What are the benefits of effective final quality control in PCB manufacturing?
The benefits of effective final quality control in PCB manufacturing include ensuring functionality, preventing failures, reducing costs, and improving customer satisfaction. It helps ensure that the PCBs meet all the specified requirements, including functionality, reliability, and safety.
Conclusion
Final quality control is a critical step in PCB manufacturing that ensures the quality, reliability, and safety of the finished products. It involves various inspection and testing methods, such as visual inspection, AOI, X-ray inspection, ICT, functional testing, burn-in testing, and environmental testing. To ensure effective final quality control, PCB manufacturers should follow best practices, such as establishing clear specifications and standards, implementing a robust quality management system, using appropriate inspection and testing methods, training and certifying personnel, and maintaining proper documentation.
By investing in effective final quality control, PCB manufacturers can reduce defects, prevent failures, improve customer satisfaction, and enhance their reputation in the industry. As the demand for high-quality PCBs continues to grow, manufacturers who prioritize quality control will be well-positioned to meet the evolving needs of their customers and stay ahead of the competition.
Here is a sample table to visualize some of the key inspection and testing methods used in PCB quality control:
Method | Type | Purpose | Defects Detected |
---|---|---|---|
Visual Inspection | Inspection | Identify visible defects | Scratches, cracks, discoloration |
AOI | Inspection | Identify surface defects | Missing/misaligned components, solder bridges |
X-Ray Inspection | Inspection | Identify internal defects | Voids, cracks, insufficient solder |
ICT | Testing | Test component functionality | Open circuits, short circuits, incorrect values |
Functional Testing | Testing | Test overall board functionality | Software bugs, compatibility issues |
Burn-In Testing | Testing | Identify early failures/weaknesses | Manufacturing defects, component issues |
Environmental Testing | Testing | Evaluate durability/reliability | Design weaknesses, material incompatibilities |
0 Comments