1. Choose the Right Materials for FlexPCB-Manufacturing
Selecting the appropriate materials is crucial for successful FlexPCB manufacturing. The most common materials used for flexible substrates are polyimide (PI) and polyester (PET). PI is known for its excellent thermal and chemical resistance, while PET is more cost-effective and suitable for less demanding applications.
Material | Advantages | Disadvantages |
---|---|---|
Polyimide (PI) | High thermal resistance, High chemical resistance, Excellent mechanical properties | More expensive, Requires higher processing temperatures |
Polyester (PET) | Cost-effective, Lower processing temperatures, Good electrical properties | Lower thermal resistance, Lower chemical resistance |
Copper Foil Selection
In addition to the substrate material, choosing the right copper foil is essential. Rolled annealed (RA) copper foil is the most common choice for FlexPCBs due to its high ductility and flexibility. Electrodeposited (ED) copper foil is another option, offering better adhesion to the substrate but lower ductility compared to RA foil.
2. Design for Manufacturability (DFM)
Designing FlexPCBs with manufacturability in mind is essential for a perfect manufacturing process. Consider the following DFM guidelines:
- Minimize the number of layers to reduce complexity and cost
- Use larger trace widths and spacing to accommodate the flexing motion
- Avoid sharp corners and use rounded traces to reduce stress concentration
- Incorporate strain relief features, such as curved traces and teardrops, to improve flexibility
- Define the bend radius and bend area to ensure proper flexing performance
3. Optimize the Layer Stack-Up
The layer stack-up of a FlexPCB plays a significant role in its performance and manufacturability. A typical FlexPCB Stack-up consists of a flexible substrate, adhesive layers, copper layers, and cover layers. Consider the following tips when optimizing the layer stack-up:
- Use symmetrical stack-ups to minimize warpage and ensure even stress distribution
- Incorporate shielding layers to reduce electromagnetic interference (EMI)
- Use thin substrates and copper layers to improve flexibility
- Select appropriate adhesives with good bonding strength and flexibility
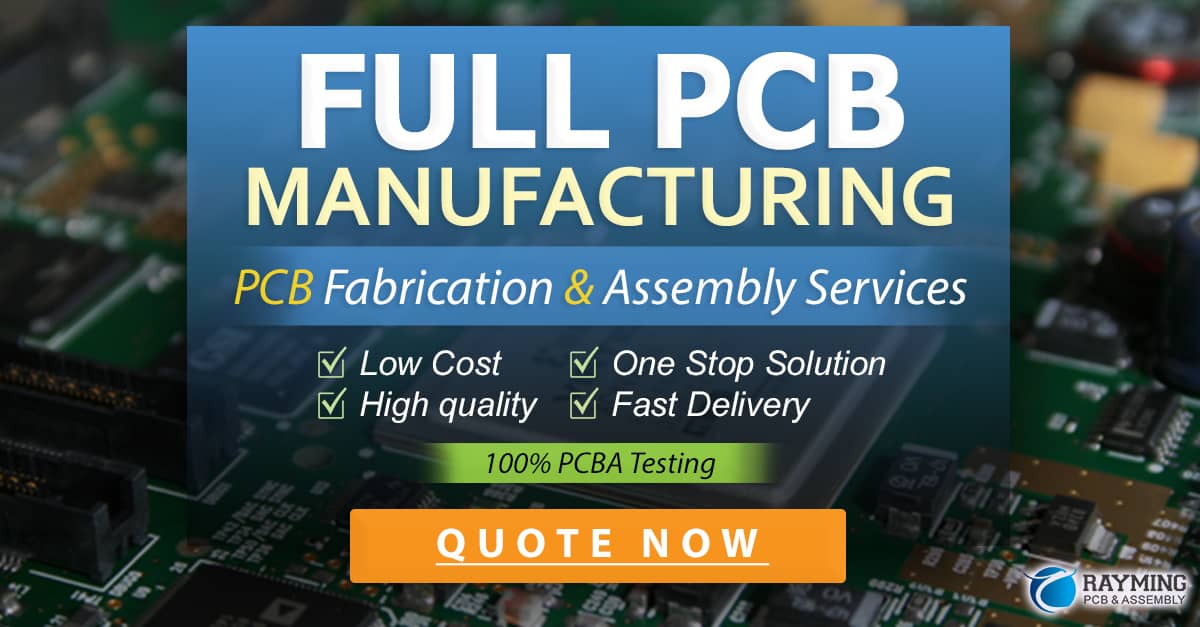
4. Implement Controlled Impedance
Controlling the impedance of FlexPCBs is crucial for high-speed applications. To achieve controlled impedance, consider the following factors:
- Use appropriate dielectric materials with consistent thickness and dielectric constant
- Adjust trace width and spacing to achieve the desired impedance
- Incorporate ground planes to provide a stable reference for signals
- Perform impedance simulations and measurements to verify the design
5. Use Appropriate Connectors and Terminations
Selecting the right connectors and terminations is essential for reliable connections in FlexPCBs. Consider the following guidelines:
- Choose connectors with low insertion force and high retention force
- Use surface mount connectors to minimize the stress on the FlexPCB
- Incorporate strain relief features at the connector-FlexPCB interface
- Use suitable termination methods, such as zero insertion force (ZIF) connectors or soldering
6. Implement Proper Panelization
Panelization is the process of arranging multiple FlexPCBs on a larger panel for efficient manufacturing. To implement proper panelization, consider the following tips:
- Use tab-routed or score-and-break panelization methods to minimize stress on the FlexPCBs
- Incorporate fiducial marks for accurate registration and alignment
- Use a balanced panel layout to ensure even copper distribution and minimize warpage
- Incorporate stress relief features, such as mouseholes and V-grooves, to facilitate depanelization
7. Optimize the Coverlay Application
The coverlay is a protective layer applied to the FlexPCB to insulate and protect the exposed copper traces. To optimize the coverlay application, consider the following:
- Use a coverlay material with good adhesion and flexibility properties
- Ensure proper alignment and registration of the coverlay to the FlexPCB
- Use a controlled lamination process with appropriate temperature, pressure, and time settings
- Incorporate openings in the coverlay for component pads and test points
8. Implement Rigorous Quality Control
Implementing rigorous quality control measures is essential for ensuring a perfect FlexPCB manufacturing process. Consider the following quality control practices:
- Perform incoming material inspections to verify the quality of raw materials
- Implement in-process inspections at critical stages of manufacturing
- Use automated optical inspection (AOI) systems to detect defects and anomalies
- Perform electrical testing to verify the functionality and performance of the FlexPCBs
- Conduct mechanical testing to assess the flexibility and durability of the FlexPCBs
9. Choose an Experienced FlexPCB Manufacturer
Choosing an experienced and reputable FlexPCB manufacturer is crucial for ensuring a perfect manufacturing process. Consider the following factors when selecting a FlexPCB manufacturer:
- Look for a manufacturer with a proven track record in FlexPCB manufacturing
- Ensure the manufacturer has the necessary equipment and expertise for your specific FlexPCB requirements
- Request samples and references to assess the quality of their work
- Evaluate the manufacturer’s quality control processes and certifications
- Consider the manufacturer’s lead times, pricing, and customer support
Frequently Asked Questions (FAQ)
1. What is the typical bend radius for FlexPCBs?
The bend radius of a FlexPCB depends on various factors, such as the substrate material, copper thickness, and the number of layers. As a general rule, the minimum bend radius should be at least 6 times the total thickness of the FlexPCB. However, it is essential to consult with your FlexPCB manufacturer to determine the appropriate bend radius for your specific application.
2. Can FlexPCBs be used in high-temperature environments?
Yes, FlexPCBs can be designed to withstand high-temperature environments. Polyimide (PI) substrates are commonly used for high-temperature applications due to their excellent thermal stability. PI-based FlexPCBs can typically withstand temperatures up to 260°C. However, it is crucial to consider the temperature ratings of all materials used in the FlexPCB, including adhesives, coatings, and components.
3. How do I specify the bend area on a FlexPCB?
When designing a FlexPCB, it is essential to clearly specify the bend area and the direction of the bend. This can be done by adding a bend line or a bend area outline on the design layout. The bend line should be perpendicular to the direction of the bend and should be located at the center of the bend area. It is also important to communicate the bend requirements to your FlexPCB manufacturer to ensure proper fabrication and assembly.
4. Can FlexPCBs be used for high-frequency applications?
Yes, FlexPCBs can be designed for high-frequency applications. However, it is essential to consider the specific requirements of high-frequency designs, such as controlled impedance, signal integrity, and EMI shielding. When designing FlexPCBs for high-frequency applications, use appropriate materials with low dielectric loss, implement controlled impedance techniques, and incorporate shielding layers to minimize EMI.
5. How do I choose the right adhesive for my FlexPCB?
Choosing the right adhesive for your FlexPCB depends on various factors, such as the substrate material, operating temperature, and environmental conditions. The most common adhesives used in FlexPCBs are acrylic and epoxy-based adhesives. Acrylic adhesives offer good flexibility and adhesion, while epoxy adhesives provide better thermal and chemical resistance. It is essential to consult with your FlexPCB manufacturer and adhesive supplier to select the most suitable adhesive for your specific application.
In conclusion, achieving a perfect FlexPCB manufacturing process requires careful consideration of various factors, from material selection and design for manufacturability to quality control and vendor selection. By following the nine ways discussed in this article and working closely with an experienced FlexPCB manufacturer, you can ensure the success of your FlexPCB projects.
0 Comments