Introduction
Printed Circuit Board (PCB) soldering is a crucial process in the manufacturing of electronic devices. It involves the attachment of electronic components to the PCB using solder, a metal alloy that melts at a relatively low temperature. However, the soldering process is not always perfect, and various defects can occur, leading to malfunctions or complete failure of the electronic device. In this article, we will discuss nine common PCB Soldering defects and their solutions.
What is PCB Soldering?
PCB soldering is the process of joining electronic components to a printed circuit board using solder. The solder is typically a metal alloy made of tin, lead, and sometimes silver or copper. The soldering process involves heating the solder until it melts and then applying it to the connection points between the electronic components and the PCB. Once the solder cools and solidifies, it creates a strong electrical and mechanical connection between the components and the PCB.
Why is PCB Soldering Important?
PCB soldering is essential for the proper functioning of electronic devices. It ensures that the electronic components are securely attached to the PCB and that there is a reliable electrical connection between them. Poor soldering can lead to various problems, such as intermittent connections, short circuits, and even complete failure of the device. Therefore, it is crucial to ensure that the soldering process is done correctly and that any defects are identified and corrected before the device is put into use.
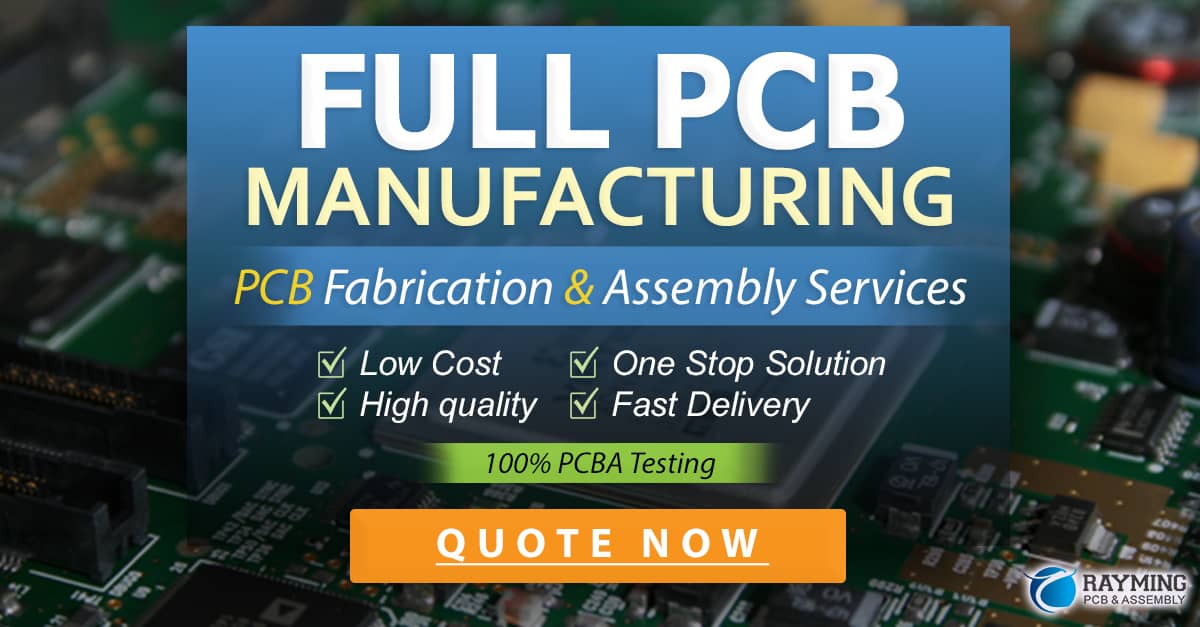
Common PCB Soldering Defects
1. Bridging
Bridging is a common PCB soldering defect that occurs when solder accidentally connects two or more adjacent pins or pads that should not be connected. This can happen when too much solder is applied or when the soldering iron is not properly controlled. Bridging can cause short circuits and lead to malfunctions or complete failure of the electronic device.
Causes of Bridging
- Applying too much solder
- Improper control of the soldering iron
- Incorrect placement of components
- Insufficient spacing between pins or pads
Solutions for Bridging
- Use the correct amount of solder
- Ensure proper control of the soldering iron
- Double-check component placement before soldering
- Increase spacing between pins or pads if possible
- Use a solder wick or desoldering pump to remove excess solder
2. Cold Solder Joints
Cold solder joints occur when the solder does not melt completely or when it does not adhere properly to the surfaces being joined. This can happen when the soldering iron is not hot enough, when the surfaces are not clean, or when the solder is of poor quality. Cold solder joints can cause intermittent connections and lead to malfunctions or complete failure of the electronic device.
Causes of Cold Solder Joints
- Insufficient heat from the soldering iron
- Dirty or oxidized surfaces
- Poor quality solder
- Incorrect soldering technique
Solutions for Cold Solder Joints
- Ensure that the soldering iron is hot enough
- Clean and remove any oxidation from the surfaces before soldering
- Use high-quality solder
- Use the correct soldering technique (apply heat to both surfaces and then apply solder)
- Reheat the joint and apply additional solder if necessary
3. Excessive Solder
Excessive solder, also known as solder buildup or solder balling, occurs when too much solder is applied to a connection point. This can happen when the soldering iron is held in place for too long or when too much solder is used. Excessive solder can cause short circuits and lead to malfunctions or complete failure of the electronic device.
Causes of Excessive Solder
- Holding the soldering iron in place for too long
- Using too much solder
- Incorrect soldering technique
Solutions for Excessive Solder
- Use the correct amount of solder
- Ensure proper control of the soldering iron (apply heat briefly and then remove)
- Use a solder wick or desoldering pump to remove excess solder
4. Insufficient Solder
Insufficient solder occurs when not enough solder is applied to a connection point. This can happen when too little solder is used or when the soldering iron is not held in place long enough. Insufficient solder can cause weak connections and lead to intermittent malfunctions or complete failure of the electronic device.
Causes of Insufficient Solder
- Using too little solder
- Not holding the soldering iron in place long enough
- Incorrect soldering technique
Solutions for Insufficient Solder
- Use the correct amount of solder
- Ensure that the soldering iron is held in place long enough to melt the solder completely
- Use the correct soldering technique (apply heat to both surfaces and then apply solder)
- Reheat the joint and apply additional solder if necessary
5. Lifted Pads
Lifted pads occur when the copper pad on the PCB separates from the board during the soldering process. This can happen when the soldering iron is held in place for too long or when too much force is applied to the pad. Lifted pads can cause open circuits and lead to malfunctions or complete failure of the electronic device.
Causes of Lifted Pads
- Holding the soldering iron in place for too long
- Applying too much force to the pad
- Poor quality PCB or copper pad
- Incorrect soldering technique
Solutions for Lifted Pads
- Use the correct soldering technique (apply heat briefly and then remove)
- Avoid applying excessive force to the pad
- Use high-quality PCBs and ensure that the copper pads are properly adhered to the board
- If a pad is lifted, it may be possible to repair it using a conductive epoxy or by soldering a small wire to the pad and the adjacent trace
6. Tombstoning
Tombstoning, also known as Manhattan effect or Stonehenge effect, occurs when a surface-mount component stands up on one end during the soldering process. This can happen when there is an uneven distribution of solder on the pads or when the component is not properly seated on the pads before soldering. Tombstoning can cause open circuits and lead to malfunctions or complete failure of the electronic device.
Causes of Tombstoning
- Uneven distribution of solder on the pads
- Improper seating of the component on the pads
- Incorrect placement of the component
- Incorrect soldering technique
Solutions for Tombstoning
- Ensure that there is an even distribution of solder on the pads
- Properly seat the component on the pads before soldering
- Double-check component placement before soldering
- Use the correct soldering technique (apply heat to both pads and then apply solder)
- If tombstoning occurs, it may be possible to reflow the solder and reseat the component
7. Solder Balls
Solder balls are small spheres of solder that can form on the surface of the PCB or on the components during the soldering process. They can occur when there is an excess of solder or flux, or when the soldering temperature is too high. Solder balls can cause short circuits and lead to malfunctions or complete failure of the electronic device.
Causes of Solder Balls
- Excess solder or flux
- High soldering temperature
- Incorrect soldering technique
Solutions for Solder Balls
- Use the correct amount of solder and flux
- Ensure that the soldering temperature is not too high
- Use the correct soldering technique (apply heat briefly and then remove)
- Clean the PCB and components thoroughly after soldering to remove any excess flux or solder
8. Solder Webbing
Solder webbing, also known as solder bridges, occurs when solder flows between adjacent pins or pads creating a conductive path where none should exist. This can happen when too much solder is applied or when the soldering iron is not properly controlled. Solder webbing can cause short circuits and lead to malfunctions or complete failure of the electronic device.
Causes of Solder Webbing
- Applying too much solder
- Improper control of the soldering iron
- Incorrect placement of components
- Insufficient spacing between pins or pads
Solutions for Solder Webbing
- Use the correct amount of solder
- Ensure proper control of the soldering iron
- Double-check component placement before soldering
- Increase spacing between pins or pads if possible
- Use a solder wick or desoldering pump to remove the solder bridge
9. Dry Joints
Dry joints occur when the solder does not flow properly onto the surfaces being joined, resulting in a dull, porous, or grainy appearance. This can happen when the surfaces are not clean, when the soldering iron is not hot enough, or when the solder is of poor quality. Dry joints can cause intermittent connections and lead to malfunctions or complete failure of the electronic device.
Causes of Dry Joints
- Dirty or oxidized surfaces
- Insufficient heat from the soldering iron
- Poor quality solder
- Incorrect soldering technique
Solutions for Dry Joints
- Clean and remove any oxidation from the surfaces before soldering
- Ensure that the soldering iron is hot enough
- Use high-quality solder
- Use the correct soldering technique (apply heat to both surfaces and then apply solder)
- Reheat the joint and apply additional solder if necessary
PCB Soldering Defects and Their Causes
Defect | Causes |
---|---|
Bridging | – Applying too much solder – Improper control of the soldering iron – Incorrect placement of components – Insufficient spacing between pins or pads |
Cold Solder Joints | – Insufficient heat from the soldering iron – Dirty or oxidized surfaces – Poor quality solder – Incorrect soldering technique |
Excessive Solder | – Holding the soldering iron in place for too long – Using too much solder – Incorrect soldering technique |
Insufficient Solder | – Using too little solder – Not holding the soldering iron in place long enough – Incorrect soldering technique |
Lifted Pads | – Holding the soldering iron in place for too long – Applying too much force to the pad – Poor quality PCB or copper pad – Incorrect soldering technique |
Tombstoning | – Uneven distribution of solder on the pads – Improper seating of the component on the pads – Incorrect placement of the component – Incorrect soldering technique |
Solder Balls | – Excess solder or flux – High soldering temperature – Incorrect soldering technique |
Solder Webbing | – Applying too much solder – Improper control of the soldering iron – Incorrect placement of components – Insufficient spacing between pins or pads |
Dry Joints | – Dirty or oxidized surfaces – Insufficient heat from the soldering iron – Poor quality solder – Incorrect soldering technique |
Frequently Asked Questions (FAQ)
1. What is the most common PCB soldering defect?
The most common PCB soldering defect is bridging, which occurs when solder accidentally connects two or more adjacent pins or pads that should not be connected.
2. Can PCB soldering defects be repaired?
Yes, most PCB soldering defects can be repaired using various techniques such as solder wick, desoldering pump, or conductive epoxy. However, prevention is always better than cure, so it is essential to use the correct soldering techniques and materials to avoid defects in the first place.
3. What is the best way to prevent PCB soldering defects?
The best way to prevent PCB soldering defects is to use the correct soldering techniques and materials. This includes using the right amount of solder and flux, ensuring that the soldering iron is at the correct temperature, and properly cleaning and preparing the surfaces before soldering.
4. How can I tell if a solder joint is good or bad?
A good solder joint should be shiny, smooth, and concave in shape. It should also have a good mechanical and electrical connection to the surfaces being joined. A bad solder joint, on the other hand, may appear dull, porous, or grainy, and may have a weak or intermittent connection.
5. Can I use any type of solder for PCB soldering?
No, it is essential to use the correct type of solder for PCB soldering. The most common types of solder used for PCB soldering are lead-free solder (Sn-Ag-Cu) and leaded solder (Sn-Pb). It is important to choose the right solder for the specific application and to follow the manufacturer’s guidelines for use.
Conclusion
PCB soldering is a critical process in the manufacturing of electronic devices, and it is essential to ensure that it is done correctly to avoid defects and malfunctions. In this article, we have discussed nine common PCB soldering defects, their causes, and solutions. By understanding these defects and following the correct soldering techniques and materials, it is possible to minimize the occurrence of defects and ensure the proper functioning of electronic devices.
0 Comments