Introduction to PCB Assembly
Printed Circuit Board (PCB) assembly is a crucial process in the manufacturing of electronic devices. It involves the placement and soldering of electronic components onto a printed circuit board, which serves as the backbone of the device. The PCB assembly process can be complex and time-consuming, requiring precision and attention to detail to ensure the final product functions as intended.
In this article, we will guide you through the 7 essential steps to finish electronic PCB assembly, from designing the PCB to testing the final product. By following these steps, you can ensure a smooth and efficient PCB assembly process, resulting in high-quality electronic devices.
Step 1: PCB Design and Layout
Importance of PCB Design
The first step in the PCB assembly process is designing the PCB itself. This step is crucial as it lays the foundation for the entire assembly process. A well-designed PCB can simplify the assembly process, reduce the risk of errors, and ensure optimal performance of the final product.
Key Considerations in PCB Design
When designing a PCB, there are several key considerations to keep in mind:
- Component placement: Components should be placed in a logical and accessible manner, taking into account factors such as heat dissipation and signal integrity.
- Trace routing: Traces should be routed efficiently to minimize signal interference and ensure proper connectivity between components.
- Manufacturability: The PCB design should be optimized for manufacturability, taking into account factors such as minimum trace widths and clearances, and the capabilities of the manufacturing process.
PCB Design Software
There are several software tools available for PCB design, ranging from free open-source options to high-end commercial solutions. Some popular PCB design software include:
Software | Description | Price |
---|---|---|
KiCad | Open-source PCB design software with a wide range of features | Free |
Eagle | Popular PCB design software with a large user community | $169 – $820 |
Altium Designer | High-end PCB design software with advanced features for complex designs | $8,195 – $16,995 |
Step 2: PCB Fabrication
Overview of PCB Fabrication Process
Once the PCB design is complete, the next step is to fabricate the physical PCB. This involves several sub-steps, including:
- PCB material selection: The appropriate PCB material is selected based on factors such as the intended application, environmental conditions, and cost.
- PCB layup: The PCB layers are stacked and aligned according to the design specifications.
- Drilling: Holes are drilled into the PCB for through-hole components and vias.
- Plating: The drilled holes are plated with a conductive material to ensure proper connectivity between layers.
- Etching: The unnecessary copper is etched away, leaving only the desired traces and pads.
- Solder mask application: A protective solder mask is applied to the PCB to prevent short circuits and improve solderability.
- Silkscreen printing: Text and symbols are printed onto the PCB for easy identification of components and connectors.
Choosing a PCB Fabrication Service
There are many PCB fabrication services available, each with its own capabilities and pricing. When choosing a PCB fabrication service, consider the following factors:
- Turnaround time
- Pricing
- Quality and reliability
- Capabilities (e.g., minimum trace widths, number of layers)
- Customer support
Some popular PCB fabrication services include:
Service | Description | Pricing |
---|---|---|
JLCPCB | Low-cost, high-quality PCB fabrication with fast turnaround times | $2 for 10 PCBs |
PCBWay | Full-service PCB fabrication with a wide range of options | $5 for 10 PCBs |
OSH Park | High-quality, purple PCBs with a focus on open-source designs | $5 per square inch |
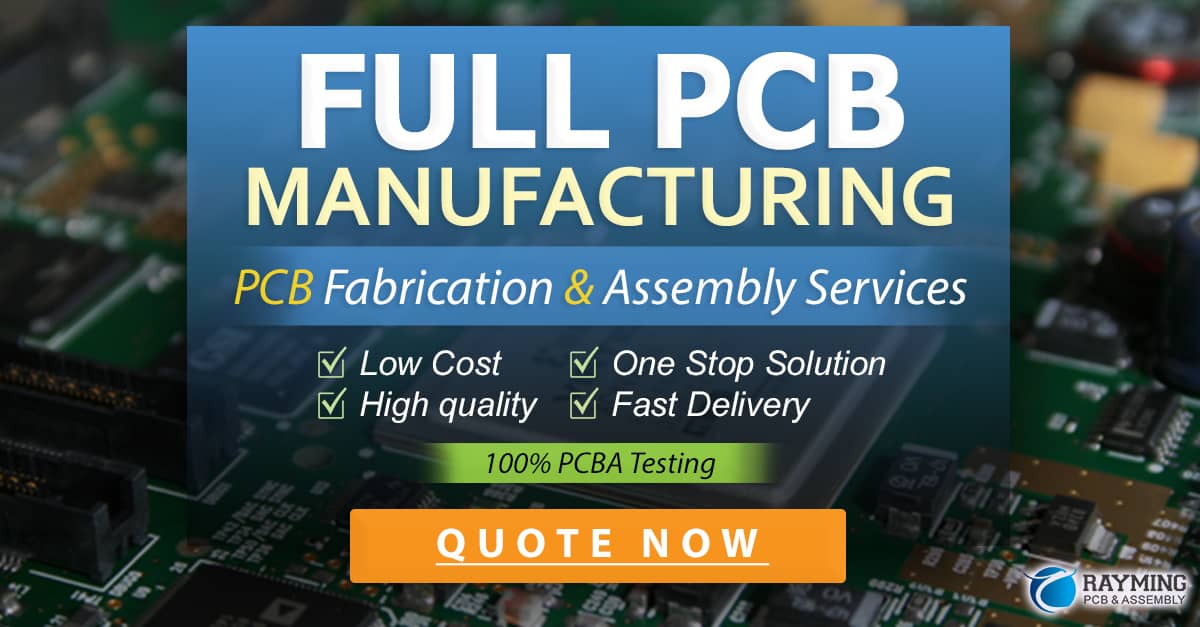
Step 3: Component Sourcing and Procurement
Importance of Component Selection
Selecting the right components for your PCB assembly is crucial for ensuring the performance, reliability, and cost-effectiveness of the final product. When selecting components, consider the following factors:
- Functionality: Ensure that the component meets the requirements of your design.
- Quality: Choose components from reputable manufacturers to ensure reliability and consistency.
- Cost: Consider the cost of the component and its impact on the overall cost of the assembly.
- Availability: Ensure that the component is readily available and can be procured in the required quantities.
Component Procurement Strategies
There are several strategies for procuring components for your PCB assembly:
- In-house procurement: If you have the resources and expertise, you can procure components directly from manufacturers or distributors.
- Outsourcing to a PCB assembly service: Many PCB assembly services offer component procurement as part of their package, simplifying the process for you.
- Consignment: You can purchase the components yourself and consign them to the PCB assembly service for use in your assembly.
Component Storage and Handling
Proper storage and handling of components is essential to ensure their quality and reliability. Components should be stored in a cool, dry place, away from sources of heat and moisture. Electrostatic discharge (ESD) protection should be used when handling sensitive components to prevent damage.
Step 4: PCB Assembly
Overview of PCB Assembly Process
The PCB assembly process involves several sub-steps, including:
- Solder paste application: Solder paste is applied to the pads on the PCB where components will be placed.
- Component placement: Components are placed onto the PCB, either manually or using automated pick-and-place machines.
- Reflow soldering: The PCB is heated in a reflow oven, melting the solder paste and forming a permanent bond between the components and the PCB.
- Inspection: The assembled PCB is inspected for any defects or errors, such as misaligned components or solder bridges.
- Rework: Any defects or errors found during inspection are corrected through rework, such as replacing components or resoldering connections.
PCB Assembly Methods
There are two main methods for PCB assembly:
- Through-hole assembly: Components with long leads are inserted through holes in the PCB and soldered in place. This method is slower and more labor-intensive but is suitable for larger components and higher-power applications.
- Surface-mount assembly: Components are placed directly onto pads on the surface of the PCB and soldered in place. This method is faster and more automated but requires more precise placement and is suitable for smaller components and higher-density designs.
Choosing a PCB Assembly Service
When choosing a PCB assembly service, consider the following factors:
- Capabilities: Ensure that the service can handle your specific assembly requirements, such as component types and sizes, and assembly methods.
- Quality and reliability: Look for a service with a track record of producing high-quality assemblies and a robust quality control process.
- Turnaround time: Consider the service’s turnaround time and whether it meets your project timeline.
- Pricing: Compare pricing among different services, taking into account factors such as component procurement and minimum order quantities.
- Customer support: Choose a service with responsive and helpful customer support to ensure a smooth assembly process.
Step 5: Soldering
Importance of Soldering
Soldering is a crucial step in the PCB assembly process, as it forms the electrical and mechanical connections between components and the PCB. Proper soldering is essential for ensuring the reliability and performance of the final product.
Soldering Techniques
There are several soldering techniques used in PCB assembly:
- Hand soldering: Components are soldered manually using a soldering iron. This method is suitable for small-scale assembly or rework but is slower and more labor-intensive.
- Wave soldering: The PCB is passed over a wave of molten solder, which flows onto the pads and through-holes, forming a connection. This method is faster and more automated but is only suitable for through-hole components.
- Reflow soldering: The PCB is heated in a reflow oven, melting the solder paste and forming a connection between the components and the PCB. This method is faster and more automated and is suitable for surface-mount components.
Soldering Best Practices
To ensure proper soldering, follow these best practices:
- Use the appropriate solder type and size for your application
- Ensure that the soldering iron or oven is set to the correct temperature
- Use flux to improve solder flow and prevent oxidation
- Inspect solder joints for proper formation and connectivity
- Use ESD protection when handling sensitive components
Step 6: Inspection and Testing
Importance of Inspection and Testing
Inspection and testing are critical steps in the PCB assembly process, as they ensure that the final product functions as intended and meets quality standards. Proper inspection and testing can identify defects and errors early in the process, reducing the risk of costly rework or product failures.
Inspection Methods
There are several methods for inspecting PCB assemblies:
- Visual inspection: The assembled PCB is visually inspected for defects such as misaligned components, solder bridges, or damaged components.
- Automated optical inspection (AOI): The PCB is scanned using high-resolution cameras and image processing software to detect defects and errors.
- X-ray inspection: The PCB is scanned using X-rays to detect internal defects such as voids or cracks in solder joints.
Testing Methods
There are several methods for testing PCB assemblies:
- In-circuit testing (ICT): The PCB is connected to a test fixture that applies electrical signals to specific points on the board to test for connectivity and functionality.
- Functional testing: The PCB is powered on and tested for proper functionality, such as signal integrity and performance.
- Boundary scan testing: The PCB is tested using built-in test access points and software to detect faults and errors in the interconnections between components.
Developing a Test Plan
To ensure comprehensive and effective testing, develop a test plan that includes the following elements:
- Test objectives and requirements
- Test methods and equipment
- Test procedures and protocols
- Acceptance criteria and tolerances
- Documentation and reporting requirements
Step 7: Final Assembly and Packaging
Overview of Final Assembly
Final assembly involves the integration of the PCB assembly into the final product, such as a device enclosure or system. This step may involve additional tasks such as:
- Attaching connectors, cables, or other components
- Installing the PCB assembly into the enclosure or system
- Sealing or protecting the PCB assembly from environmental factors
Packaging Considerations
Proper packaging is essential for protecting the PCB assembly during storage, transport, and handling. Consider the following factors when selecting packaging materials and methods:
- Protection from ESD and physical damage
- Moisture and corrosion resistance
- Ease of handling and storage
- Compliance with shipping and handling regulations
Documentation and Labeling
Proper documentation and labeling are essential for ensuring traceability and ease of use for the final product. Include the following elements in your documentation and labeling:
- Part numbers and revisions
- Serial numbers or batch identifiers
- Assembly instructions or user manuals
- Compliance and certification markings
Conclusion
PCB assembly is a complex and multi-step process that requires careful planning, execution, and quality control. By following these 7 steps and best practices, you can ensure a smooth and efficient assembly process, resulting in high-quality and reliable electronic products.
Frequently Asked Questions
-
What is the difference between through-hole and surface-mount assembly?
Through-hole assembly involves inserting component leads through holes in the PCB and soldering them in place, while surface-mount assembly involves placing components directly onto pads on the surface of the PCB and soldering them in place. Surface-mount assembly is faster and more automated, while through-hole assembly is more suitable for larger components and higher-power applications. -
What factors should I consider when choosing a PCB fabrication service?
When choosing a PCB fabrication service, consider factors such as turnaround time, pricing, quality and reliability, capabilities (e.g., minimum trace widths, number of layers), and customer support. -
What are some common defects that can occur during PCB assembly?
Common defects in PCB assembly include misaligned components, solder bridges, insufficient or excessive solder, damaged components, and cold solder joints. -
What are some best practices for soldering in PCB assembly?
To ensure proper soldering, use the appropriate solder type and size for your application, ensure that the soldering iron or oven is set to the correct temperature, use flux to improve solder flow and prevent oxidation, inspect solder joints for proper formation and connectivity, and use ESD protection when handling sensitive components. -
What should I include in my PCB assembly documentation and labeling?
PCB assembly documentation and labeling should include part numbers and revisions, serial numbers or batch identifiers, assembly instructions or user manuals, and compliance and certification markings to ensure traceability and ease of use for the final product.
0 Comments