Introduction to PCB Manufacturing
Printed Circuit Boards (PCBs) are the backbone of modern electronics, providing a platform for interconnecting electronic components in a compact and efficient manner. As technology advances, the demand for more complex and dense PCB designs has increased, leading to the development of multi-layer PCBs. Among these, 16 layers PCB has emerged as a popular choice for high-performance applications that require a high degree of functionality and reliability.
What is a 16 Layers PCB?
A 16 layers PCB is a type of multi-layer printed circuit board that consists of 16 conductive layers sandwiched between insulating layers. These layers are interconnected through vias, which are small holes drilled through the board and plated with conductive material. The increased number of layers allows for a higher density of components and more complex routing, making 16 layers PCBs ideal for applications that require high speed, high frequency, and high power.
Advantages of 16 Layers PCBs
-
Increased Functionality: With 16 layers, designers have more space to route traces and place components, enabling more complex and feature-rich designs.
-
Improved Signal Integrity: The additional layers help to reduce crosstalk and electromagnetic interference (EMI), ensuring cleaner and more stable signals.
-
Better Heat Dissipation: The increased number of layers allows for better thermal management, as heat can be spread more evenly across the board.
-
Reduced Size and Weight: By stacking layers vertically, 16 layers PCBs can achieve higher density while maintaining a smaller footprint and lower weight compared to equivalent single or double-layer boards.
Choosing the Right 16 Layers PCB Manufacturer
When it comes to manufacturing 16 layers PCBs, choosing the right PCB manufacturer is crucial. Not all manufacturers have the capability and expertise to produce high-quality 16 layers PCBs consistently. Here are some key factors to consider when selecting a 16 layers PCB manufacturer:
Experience and Expertise
Look for a manufacturer with a proven track record of producing 16 layers PCBs. They should have the necessary equipment, processes, and skilled personnel to handle the complexity of multi-layer PCB fabrication. Ask for references and samples of their previous work to assess their capabilities.
Quality Control and Certifications
Ensure that the manufacturer has robust quality control processes in place, including automated optical inspection (AOI), X-ray inspection, and electrical testing. They should also hold relevant industry certifications, such as ISO 9001, UL, and RoHS, to demonstrate their commitment to quality and compliance with international standards.
Turnaround Time and Pricing
16 layers PCB manufacturing is a complex and time-consuming process, so it’s important to choose a manufacturer that can deliver on time and within budget. Look for a manufacturer that offers competitive pricing without compromising on quality, and has a clear and transparent pricing structure.
Customer Support and Communication
Good communication is key to a successful PCB manufacturing project. Choose a manufacturer that is responsive, proactive, and willing to work closely with you throughout the design and manufacturing process. They should provide timely updates and be available to answer any questions or concerns you may have.
16 Layers PCB Manufacturing Process
The manufacturing process for 16 layers PCBs is highly complex and requires specialized equipment and expertise. Here’s a brief overview of the key steps involved:
-
Design and Layout: The PCB design is created using specialized software, taking into account the specific requirements of the 16 layers construction.
-
Material Selection: High-quality substrate materials, such as FR-4, Rogers, or Isola, are selected based on the application’s requirements for dielectric constant, loss tangent, and thermal stability.
-
Inner Layer Fabrication: The inner layers are imaged, etched, and inspected using automated equipment to ensure precise alignment and registration.
-
Lamination: The inner layers are stacked and laminated together under high pressure and temperature to form a solid board.
-
Drilling: Holes are drilled through the board to create vias and mounting holes for components.
-
Plating: The holes are plated with copper to create electrical connections between layers.
-
Outer Layer Fabrication: The outer layers are imaged, etched, and inspected, just like the inner layers.
-
Solder Mask and Silkscreen: A protective solder mask is applied to the board, and silkscreen legends are printed to identify components and connectors.
-
Surface Finish: A surface finish, such as HASL, ENIG, or OSP, is applied to protect the exposed copper and enhance solderability.
-
Electrical Testing: The completed board undergoes rigorous electrical testing to ensure functionality and reliability.
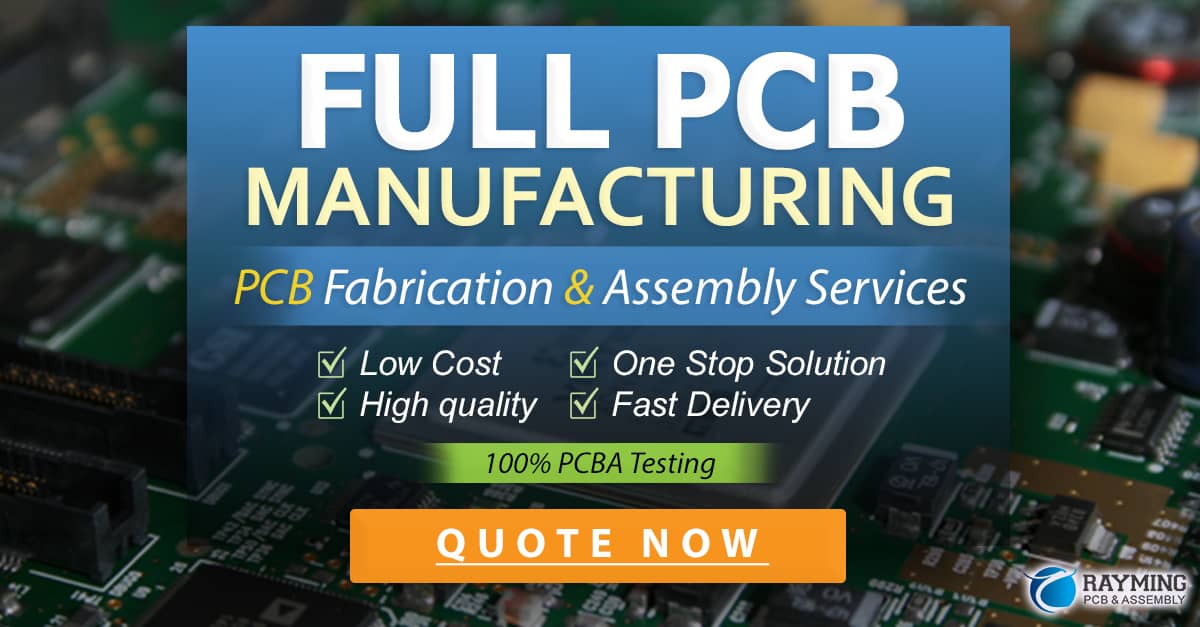
Applications of 16 Layers PCBs
16 layers PCBs are used in a wide range of industries and applications that require high performance, reliability, and functionality. Some common applications include:
-
Telecommunications: 16 layers PCBs are used in high-speed networking equipment, such as routers, switches, and base stations, to handle the complex routing and high-frequency signals.
-
Aerospace and Defense: In military and aerospace applications, 16 layers PCBs are used in radar systems, avionics, and satellite communications, where reliability and performance are critical.
-
Medical Devices: Advanced medical equipment, such as MRI machines, CT scanners, and patient monitoring systems, rely on 16 layers PCBs to process and transmit large amounts of data accurately and reliably.
-
Industrial Automation: In industrial control systems and robotics, 16 layers PCBs are used to integrate various sensors, actuators, and communication interfaces in a compact and robust package.
-
Consumer Electronics: High-end consumer devices, such as gaming consoles, smartphones, and smart TVs, use 16 layers PCBs to achieve advanced features and functionality in a small form factor.
Frequently Asked Questions (FAQ)
-
Q: What is the typical turnaround time for 16 layers PCB manufacturing?
A: The turnaround time for 16 layers PCB manufacturing can vary depending on the complexity of the design, the quantity ordered, and the manufacturer’s capacity. Typically, it can range from 2 to 4 weeks, but some manufacturers may offer expedited services for faster delivery. -
Q: How much does a 16 layers PCB cost?
A: The cost of a 16 layers PCB depends on several factors, such as the size of the board, the materials used, the quantity ordered, and the complexity of the design. As a rough estimate, a single 16 layers PCB can cost anywhere from $100 to $1000 or more, depending on these factors. -
Q: Can 16 layers PCBs be manufactured with impedance control?
A: Yes, 16 layers PCBs can be manufactured with impedance control to ensure consistent and reliable signal transmission. This is particularly important for high-speed and high-frequency applications, where signal integrity is critical. -
Q: What are the common materials used for 16 layers PCBs?
A: The most common materials used for 16 layers PCBs are FR-4, Rogers, and Isola. FR-4 is a standard glass-reinforced epoxy laminate that offers good mechanical and electrical properties at a reasonable cost. Rogers and Isola are high-performance materials that offer better dielectric properties and thermal stability for demanding applications. -
Q: Can 16 layers PCBs be manufactured with blind and buried vias?
A: Yes, 16 layers PCBs can be manufactured with blind and buried vias to achieve higher density and more complex routing. Blind vias connect an outer layer to an inner layer, while buried vias connect two or more inner layers without reaching the outer layers. However, these advanced features can increase the cost and complexity of the manufacturing process.
Conclusion
16 layers PCBs are a testament to the advancements in PCB manufacturing technology, enabling the creation of highly complex and dense electronic systems. By offering increased functionality, improved signal integrity, better heat dissipation, and reduced size and weight, 16 layers PCBs have become a critical component in various industries, from telecommunications and aerospace to medical devices and consumer electronics.
When choosing a 16 layers PCB manufacturer, it’s essential to consider factors such as experience, quality control, turnaround time, pricing, and customer support. By selecting a reputable and capable manufacturer, you can ensure that your 16 layers PCBs are manufactured to the highest standards of quality and reliability, enabling your products to perform at their best.
As technology continues to evolve, the demand for even more complex and advanced PCBs is likely to grow. 16 layers PCB Manufacturers will need to stay at the forefront of innovation, investing in new materials, processes, and equipment to meet the ever-increasing requirements of their customers. By doing so, they can help to enable the next generation of electronic devices and systems that will shape our world in the years to come.
Layer Count | Typical Applications | Advantages | Disadvantages |
---|---|---|---|
1-2 | Simple electronic devices, such as LED lights and power banks | Low cost, easy to design and manufacture | Limited functionality and routing options |
4 | Basic consumer electronics, such as smartphones and laptops | Increased functionality and routing options compared to 1-2 layers | Still limited in terms of density and complexity |
6-8 | Advanced consumer electronics, automotive, and industrial control systems | Higher density and complexity, improved signal integrity | Increased cost and manufacturing complexity compared to 4 layers |
10-12 | High-performance networking equipment, medical devices, and aerospace systems | Even higher density and complexity, better signal integrity and thermal management | Further increased cost and manufacturing complexity |
14-16 | Cutting-edge applications in telecommunications, military, and advanced medical equipment | Highest density and complexity, best signal integrity and thermal management | Highest cost and manufacturing complexity, longer turnaround times |
As the table above illustrates, the choice of layer count in a PCB is a trade-off between functionality, performance, cost, and manufacturing complexity. 16 layers PCBs offer the highest level of performance and functionality, but also come with the highest cost and complexity. Ultimately, the choice of layer count depends on the specific requirements and constraints of the application at hand.
0 Comments