Introduction to 12 Layer PCBs
12 layer printed circuit boards (PCBs) are complex, high-density boards used in advanced electronic applications that require a large number of interconnections. These boards have 12 conductive copper layers laminated together with insulating material in between each layer. The multiple layers allow for a higher density of components and traces compared to simpler 2 or 4 layer boards.
12 layer PCBs are used in applications such as:
– High-performance computing
– Telecommunications equipment
– Medical devices
– Aerospace and defense systems
– Complex industrial controls
Manufacturing 12 layer PCBs requires specialized equipment, precise processes, and expert PCB design and engineering. This article will cover the key aspects of 12 layer PCB manufacturing and provide an overview of some leading PCB Manufacturers offering 12 layer fabrication services.
Advantages of 12 Layer PCBs
The main advantages of using a 12 layer PCB include:
-
Higher component density: The 12 conductive layers allow a large number of components to be mounted on a relatively small board size. This enables miniaturization of complex electronics.
-
Increased interconnectivity: With 12 layers to route traces, the board can accommodate a high number of interconnections between components. This is essential for high-speed digital designs.
-
Better signal integrity: The ground planes and power planes in a 12 layer stackup provide effective shielding and help maintain signal integrity for sensitive high-frequency circuits.
-
Improved thermal management: Multiple copper layers help conduct heat away from hot components mounted on the board. Some inner layers can be designed as heat spreading planes.
-
Reliability: 12 layer PCBs built by a quality manufacturer offer high reliability for mission-critical applications that require a long operating life.
12 Layer PCB Stackup
The arrangement of copper, insulating, and bonding layers in a 12 layer PCB is called the stackup. A typical 12 layer stackup consists of:
- Top layer: component side, surface mount pads
- Layer 2: signal
- Layer 3: signal
- Layer 4: signal
- Layer 5: ground plane
- Layer 6: signal
- Layer 7: signal
- Layer 8: signal
- Layer 9: power plane
- Layer 10: signal
- Layer 11: signal
- Bottom layer: solder side, surface mount pads
The signal layers route traces to interconnect components. The ground and power planes provide shielding and power distribution. Insulating dielectric material separates the conductive layers. Microvias are used to interconnect between layers.
Here is an example 12 layer stackup with layer thicknesses:
Layer | Copper Thickness (oz) | Dielectric Thickness (mil) |
---|---|---|
Top | 1 | – |
Layer 2 | 0.5 | 4 |
Layer 3 | 0.5 | 4 |
Layer 4 | 0.5 | 4 |
Layer 5 | 1 | 8 |
Layer 6 | 0.5 | 4 |
Layer 7 | 0.5 | 4 |
Layer 8 | 0.5 | 4 |
Layer 9 | 1 | 8 |
Layer 10 | 0.5 | 4 |
Layer 11 | 0.5 | 4 |
Bottom | 1 | – |
Impedance control is critical when designing a 12 layer stackup. The dielectric material and thickness must be carefully selected to achieve the target impedance for each signal layer. PCB manufacturers usually provide stackup design assistance to ensure the finished board will meet specifications.
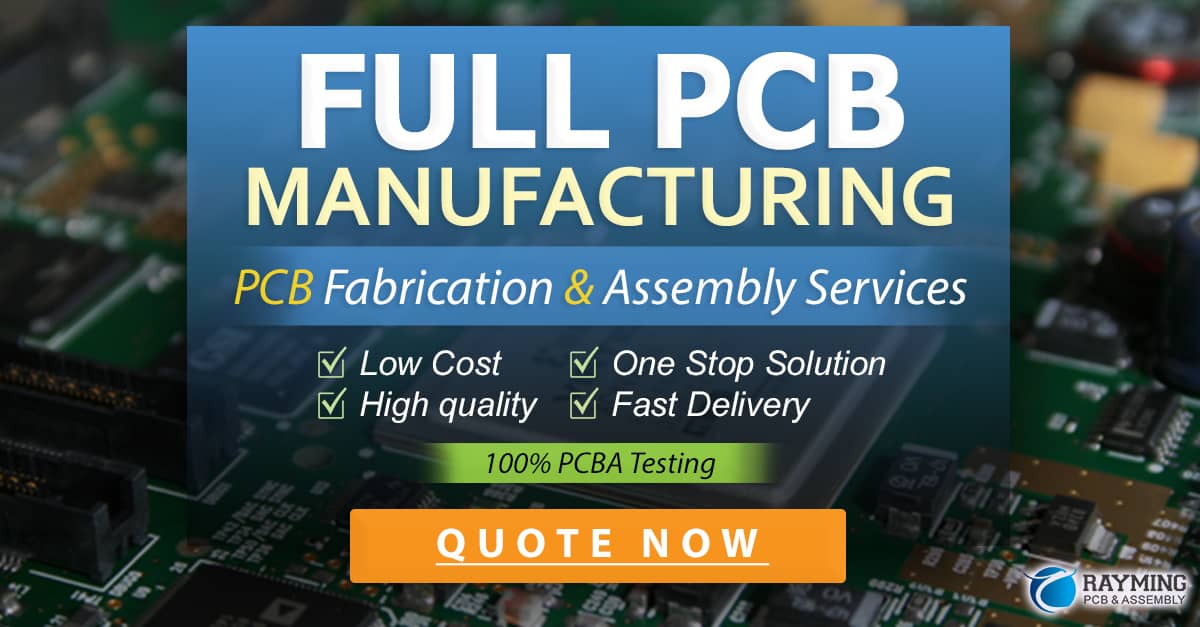
12 Layer PCB Manufacturing Process
The manufacturing process for a 12 layer PCB is complex and requires precision at each step to ensure a high quality board. The key steps in the process are:
-
Design and Engineering: The customer’s design files are imported into PCB CAD software. The manufacturer’s engineers perform design rule checks (DRC) and work with the customer to finalize the stackup and material selections.
-
Imaging and Etching: The inner layer traces are imaged onto copper clad laminate using photoresist and high resolution laser direct imaging (LDI). The unwanted copper is chemically etched away.
-
Lamination: The etched inner layers are stacked with insulating prepreg and copper foil for the outer layers. This layup is laminated under high temperature and pressure in a vacuum press to fuse into a solid board.
-
Drilling: The laminated board is drilled to create vias and through holes. High-speed computer numerical control (CNC) drilling machines are used for precision and to minimize stresses on the board. Laser drilling is used for microvias.
-
Plating: The drilled board is plated with copper to form interconnections between layers. Additional finishing metals like nickel and gold are also plated for protection and improved solderability.
-
Outer Layer Imaging and Etching: Similar to the inner layer process, the outer layer traces are imaged and etched. A plated through hole (PTH) process is used to form conductivity in the holes.
-
Solder Mask and Silkscreen: A polymer solder mask is applied to protect the outer copper traces. Silkscreen legends are printed to label components and test points.
-
Surface Finish: The exposed metal areas are coated with a surface finish to prevent oxidation and prepare the board for assembly. Common finishes for 12 layer PCBs are ENIG (electroless nickel immersion gold), HASL (hot air solder leveling), and OSP (organic solderability preservatives).
-
Electrical Test: 100% of the finished PCBs undergo automated optical inspection (AOI) and electrical testing to verify continuity and detect any short circuits or open circuits. High-voltage testing may be performed on boards for aerospace or medical use.
-
Final Inspection and Packaging: The PCBs are given a final visual inspection and then packaged for shipment to the customer. Packaging may include ESD (electrostatic discharge) protective bags, moisture barrier bags, and vacuum sealing depending on the customer’s requirements.
Here is an overview of the 12 layer PCB fabrication process:
Careful process control and quality checks at each stage are essential to producing reliable 12 layer PCBs. Leading PCB manufacturers use automated equipment and statistical process control to maintain tight tolerances and catch any defects early.
Design Considerations for 12 Layer PCBs
Designing a 12 layer PCB requires careful planning and attention to detail to ensure manufacturability and reliable performance. Some key design considerations include:
-
Signal Integrity: High-speed signals are sensitive to noise and distortion. The PCB layout must be designed to maintain signal integrity through proper trace routing, impedance control, and shielding. Ground planes and power planes should be used strategically.
-
EMC: Electromagnetic compatibility (EMC) is critical in 12 layer PCBs to prevent interference between different signals and with external devices. Proper grounding, shielding, and filtering techniques must be used. Simulate EMC performance during design.
-
Thermal Management: With a high density of components, thermal management is a challenge in 12 layer PCBs. Use thermal simulation tools to identify hot spots and design in heat spreading copper areas or thermal vias to conduct heat to outer layers.
-
DFM: Design for manufacturability (DFM) rules must be followed to ensure the PCB can be reliably fabricated. This includes minimum trace width and spacing, hole sizes, annular rings, and solder mask clearances. Consult with the PCB manufacturer early in the design process.
-
Layer Stackup: Work with the manufacturer to design the optimal layer stackup based on the circuit requirements and material properties. Consider the dielectric constant (Dk) and dissipation factor (Df) of the laminate material.
-
Wireability: Ensure the design is routable and can accommodate the necessary interconnections. Perform 3D modeling to check for any conflicts between components, traces, and vias.
-
Test Points: Include test points in the design to facilitate automated testing and troubleshooting. Follow the manufacturer’s guidelines for test point size and spacing.
By following good PCB design practices and collaborating closely with the manufacturer, designers can create 12 layer PCBs that are high-performing, reliable, and cost-effective to manufacture.
Choosing a 12 Layer PCB Manufacturer
With the complexity of 12 layer PCBs, it is critical to select a manufacturer with the capabilities and experience to build high-quality boards. Here are some factors to consider when choosing a 12 layer PCB manufacturer:
-
Technical Capabilities: Ensure the manufacturer has experience with 12 layer PCBs and the specific materials and features required for the design. Ask about their equipment and processes for lamination, drilling, plating, and testing.
-
Quality Systems: Look for manufacturers with robust quality management systems such as ISO 9001 certification. Ask about their process controls, testing procedures, and yield rates.
-
Industry Certifications: For aerospace, defense, or medical applications, the PCB manufacturer may need specific certifications such as AS9100, NADCAP, or ISO 13485. Verify they have the necessary certifications for the end use.
-
Technical Support: The manufacturer should have experienced engineers who can provide design review, DFM feedback, and troubleshooting support. Responsiveness and clear communication are important.
-
Capacity and Lead Times: Ensure the manufacturer has sufficient capacity to meet the production volume and lead time requirements. Ask about their typical lead times for prototypes and production quantities.
-
Pricing: Get quotes from multiple manufacturers to compare pricing. However, don’t choose based on price alone – consider the total cost of ownership including quality, reliability, and support.
-
Reputation: Look for manufacturers with a track record of success and positive customer references. Check online reviews and ask for references in the specific industry.
By carefully evaluating potential 12 layer PCB manufacturers and building a strong partnership, companies can ensure a reliable supply of high-quality PCBs for their critical applications.
12 Layer PCB Manufacturers
Here are some leading PCB manufacturers offering 12 layer fabrication services:
1. TTM Technologies
TTM Technologies is a global leader in PCB manufacturing with facilities in North America, Europe, and Asia. They offer 12 layer PCBs in a variety of materials and finishes for applications including aerospace, defense, medical, and telecommunications.
2. Apex International
Apex International is a Taiwan-based PCB manufacturer with over 30 years of experience. They specialize in high-layer count PCBs up to 24 layers for advanced applications. Apex has AS9100 and NADCAP certifications for aerospace and defense.
3. Kinwong Electronic
Kinwong Electronic is a leading PCB manufacturer based in China with facilities in Shenzhen and Wuxi. They offer 12 layer PCBs with a variety of materials and finishes for consumer electronics, automotive, and industrial applications.
4. Epec Engineered Technologies
Epec Engineered Technologies is a US-based PCB manufacturer specializing in high reliability boards for aerospace, defense, and medical industries. They offer 12 layer PCBs with expertise in controlled impedance and high-speed designs.
5. PCBCart
PCBCart is a China-based PCB manufacturer offering quick-turn prototypes and low-volume production. They can fabricate 12 layer PCBs in a variety of materials and finishes with lead times as fast as 24 hours for prototypes.
When selecting a 12 layer PCB manufacturer, evaluate their specific capabilities, certifications, and experience relevant to the project requirements. Request quotes and samples to compare quality and pricing.
FAQ
What are 12 layer PCBs used for?
12 layer PCBs are used in complex electronic applications that require a high density of interconnections and components. Examples include high-performance computing, telecommunications equipment, medical devices, aerospace systems, and industrial controls.
How much do 12 layer PCBs cost?
The cost of a 12 layer PCB depends on factors such as the size, material, quantity, and turnaround time. In general, 12 layer PCBs are more expensive than 2 or 4 layer boards due to the additional materials and processing steps. As a rough estimate, a 12 layer PCB may cost $50 to $200 per board in small quantities.
What materials are used in 12 layer PCBs?
Common base materials for 12 layer PCBs include FR-4, polyimide, and high-frequency laminates such as Rogers or Isola. The copper foil is typically ½ oz or 1 oz weight. Bonding materials include standard and low-flow prepreg. The specific materials are selected based on the electrical, thermal, and mechanical requirements of the application.
How long does it take to manufacture a 12 layer PCB?
The lead time for a 12 layer PCB depends on the complexity, quantity, and manufacturer. Prototype quantities may take 2-3 weeks, while production quantities may take 4-8 weeks. Some manufacturers offer expedited services for faster turnaround times.
What are the challenges in designing 12 layer PCBs?
Key challenges in 12 layer PCB design include signal integrity, EMC, thermal management, and manufacturability. Designers must carefully plan the layer stackup, trace routing, and component placement to ensure reliable performance. Close collaboration with the PCB manufacturer is essential to ensure the design is optimized for fabrication and assembly.
Conclusion
12 layer PCBs are a critical component in many advanced electronic systems that require high interconnectivity and density. Designing and manufacturing these complex boards requires specialized expertise and capabilities.
When selecting a 12 layer PCB manufacturer, it is important to evaluate their technical capabilities, quality systems, certifications, and experience relevant to the specific application. By building a strong partnership with a reputable manufacturer, companies can ensure a reliable supply of high-quality 12 layer PCBs to meet their critical needs.
As electronic systems continue to advance in complexity and functionality, the demand for 12 layer and higher PCBs will continue to grow. Staying at the forefront of PCB design and manufacturing technology will be essential for companies to remain competitive in their industries.
0 Comments