Introduction to Micro BGA Tolerance
Micro Ball Grid Array (BGA) packages have become increasingly popular in modern electronics due to their ability to provide high-density interconnections in a small footprint. These packages are commonly used in applications that require high performance, such as smartphones, tablets, and wearable devices. However, the small size of Micro BGA packages also presents challenges in terms of PCB design and manufacturing tolerances.
In this article, we will explore the concept of Micro BGA tolerance and its importance in PCB design and manufacturing. We will discuss the various factors that influence Micro BGA tolerance, such as pad size, solder mask opening, and via placement. Additionally, we will provide guidelines and best practices for designing and manufacturing PCBs with Micro BGA packages to ensure optimal performance and reliability.
Understanding Micro BGA Packages
What is a Micro BGA Package?
A Micro BGA package is a type of surface-mount technology (SMT) package that uses an array of solder balls to provide electrical connections between the package and the PCB. The solder balls are arranged in a grid pattern on the bottom of the package, with a typical pitch (distance between the centers of adjacent balls) ranging from 0.3mm to 0.5mm.
Micro BGA packages are typically smaller than traditional BGA packages, with package sizes ranging from 2mm x 2mm to 10mm x 10mm. They are often used in applications that require high-density interconnections, such as mobile devices, wearables, and IoT devices.
Advantages of Micro BGA Packages
Micro BGA packages offer several advantages over other types of SMT packages, including:
-
High-density interconnections: Micro BGA packages can provide a large number of interconnections in a small footprint, enabling the design of compact and highly integrated electronic devices.
-
Improved electrical performance: The short interconnection paths and low inductance of Micro BGA packages can improve signal integrity and reduce electromagnetic interference (EMI).
-
Enhanced thermal performance: The large number of solder balls in a Micro BGA package provides a low-resistance thermal path, allowing for efficient heat dissipation from the package to the PCB.
-
Space savings: The small size of Micro BGA packages enables the design of compact and lightweight electronic devices, which is particularly important in mobile and wearable applications.
Challenges of Micro BGA Packages
Despite their advantages, Micro BGA packages also present several challenges in terms of PCB design and manufacturing, including:
-
Tight tolerances: The small size and fine pitch of Micro BGA packages require tight tolerances in PCB design and manufacturing to ensure proper alignment and reliable solder joints.
-
Soldering difficulties: The small size of the solder balls in a Micro BGA package can make it difficult to achieve reliable solder joints, particularly in high-volume manufacturing environments.
-
Inspection challenges: The small size and high density of Micro BGA packages can make it difficult to inspect solder joints for defects, such as bridging, voids, and opens.
-
Thermal management: The high density of Micro BGA packages can make it challenging to manage heat dissipation, particularly in applications with high power densities.
Factors Affecting Micro BGA Tolerance
Several factors can influence the tolerance of Micro BGA packages on a PCB, including:
Pad Size and Shape
The size and shape of the pads on the PCB can have a significant impact on Micro BGA tolerance. In general, larger pads can accommodate greater variations in solder ball placement, while smaller pads require tighter tolerances.
The shape of the pads can also affect Micro BGA tolerance. Circular pads are often preferred over square pads, as they can accommodate greater variations in solder ball placement and reduce the risk of bridging between adjacent pads.
Solder Mask Opening
The solder mask opening (SMO) is the area on the PCB where the solder mask has been removed to expose the copper pads. The size and shape of the SMO can affect Micro BGA tolerance, as it determines the amount of copper exposed for soldering.
In general, larger SMOs can accommodate greater variations in solder ball placement, while smaller SMOs require tighter tolerances. The shape of the SMO can also affect Micro BGA tolerance, with circular SMOs often preferred over square SMOs for the same reasons as circular pads.
Via Placement
Vias are used to provide electrical connections between layers in a PCB. The placement of vias near Micro BGA pads can affect tolerance, as they can interfere with solder ball placement and cause solder joint defects.
In general, vias should be placed at least one pad diameter away from the edge of the Micro BGA pad to minimize the risk of interference. Additionally, the use of microvias (vias with a diameter of 0.15mm or less) can help to reduce the impact of via placement on Micro BGA tolerance.
PCB Fabrication Tolerances
The tolerances of the PCB fabrication process can also affect Micro BGA tolerance. Factors such as copper thickness, solder mask thickness, and drill accuracy can all impact the accuracy of pad placement and solder joint formation.
In general, tighter PCB fabrication tolerances are required for Micro BGA packages than for larger packages. This may require the use of advanced PCB fabrication techniques, such as laser drilling and high-resolution imaging, to achieve the necessary accuracy and precision.
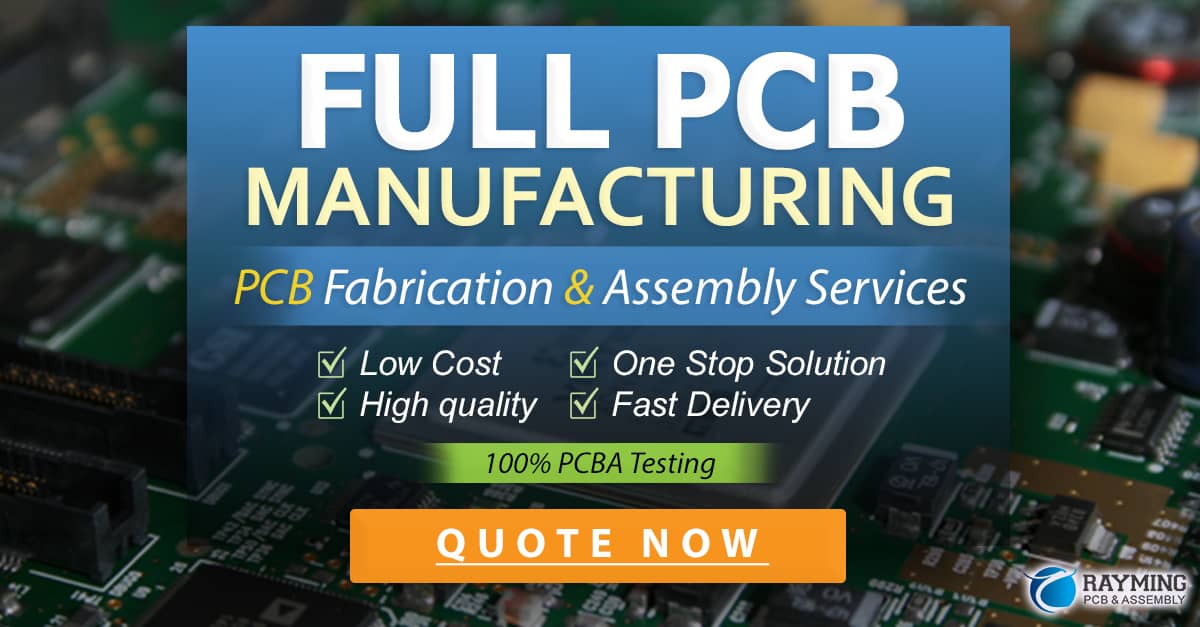
Designing for Micro BGA Tolerance
When designing PCBs with Micro BGA packages, there are several best practices that can help to ensure optimal performance and reliability:
Use Appropriate Pad Sizes and Shapes
As discussed earlier, larger pads and circular shapes can help to accommodate greater variations in solder ball placement and reduce the risk of solder joint defects. When designing pads for Micro BGA packages, it is important to consider the size and pitch of the package, as well as the capabilities of the PCB fabrication process.
The following table provides general guidelines for pad sizes and shapes for common Micro BGA pitches:
Pitch (mm) | Pad Diameter (mm) | Pad Shape |
---|---|---|
0.3 | 0.2 | Circular |
0.4 | 0.25 | Circular |
0.5 | 0.3 | Circular |
Use Appropriate Solder Mask Openings
The size and shape of the solder mask opening can also affect Micro BGA tolerance. In general, the SMO should be slightly larger than the pad size to ensure adequate coverage of the copper pad while allowing for variations in solder ball placement.
The following table provides general guidelines for SMO sizes and shapes for common Micro BGA pitches:
Pitch (mm) | SMO Diameter (mm) | SMO Shape |
---|---|---|
0.3 | 0.25 | Circular |
0.4 | 0.3 | Circular |
0.5 | 0.35 | Circular |
Minimize Via Placement Near Micro BGA Pads
As discussed earlier, the placement of vias near Micro BGA pads can affect tolerance and cause solder joint defects. When designing PCBs with Micro BGA packages, it is important to minimize the use of vias near the pads and to place them at least one pad diameter away from the edge of the pad.
If vias are necessary near Micro BGA pads, the use of microvias can help to reduce their impact on tolerance. Microvias have a smaller diameter than standard vias and can be placed closer to the pads without causing interference.
Use Appropriate PCB Fabrication Tolerances
To achieve optimal Micro BGA tolerance, it is important to use appropriate PCB fabrication tolerances. This may require the use of advanced PCB fabrication techniques, such as laser drilling and high-resolution imaging, to achieve the necessary accuracy and precision.
When specifying PCB fabrication tolerances for Micro BGA packages, it is important to consider the capabilities of the PCB fabricator and to work closely with them to ensure that the necessary tolerances can be achieved.
Use Appropriate Soldering Techniques
Achieving reliable solder joints with Micro BGA packages can be challenging, particularly in high-volume manufacturing environments. To ensure optimal solder joint formation, it is important to use appropriate soldering techniques and materials.
One common technique for soldering Micro BGA packages is to use solder paste with a fine particle size, such as Type 5 or Type 6 paste. These pastes have a smaller particle size than standard pastes and can help to achieve more precise solder ball placement and more reliable solder joints.
Another technique is to use a solder stencil with a fine pitch and a precise thickness to ensure accurate solder paste deposition. The use of a solder stencil can help to achieve more consistent solder joint formation and reduce the risk of solder joint defects.
Manufacturing Considerations for Micro BGA Tolerance
In addition to PCB design considerations, there are several manufacturing considerations that can affect Micro BGA tolerance, including:
Solder Paste Printing
The accuracy and consistency of solder paste printing can have a significant impact on Micro BGA tolerance. To ensure optimal solder paste deposition, it is important to use a solder stencil with a fine pitch and a precise thickness, as well as a solder paste with a fine particle size.
It is also important to control the printing process parameters, such as squeegee pressure, squeegee speed, and stencil release, to ensure consistent solder paste deposition across the PCB.
Component Placement
The accuracy and consistency of component placement can also affect Micro BGA tolerance. To ensure precise component placement, it is important to use a pick-and-place machine with a high degree of accuracy and repeatability.
It is also important to control the placement process parameters, such as placement force, placement speed, and placement accuracy, to ensure consistent component placement across the PCB.
Reflow Soldering
The reflow soldering process can also affect Micro BGA tolerance. To ensure optimal solder joint formation, it is important to use a reflow profile that is appropriate for the specific Micro BGA package and PCB design.
The reflow profile should be designed to achieve the necessary solder joint quality while minimizing the risk of solder joint defects, such as bridging, voids, and opens. It is also important to control the reflow process parameters, such as peak temperature, time above liquidus, and cooling rate, to ensure consistent solder joint formation across the PCB.
Inspection and Testing
Inspection and testing are critical for ensuring the reliability and performance of PCBs with Micro BGA packages. However, the small size and high density of Micro BGA packages can make inspection and testing challenging.
To ensure effective inspection and testing, it is important to use appropriate inspection and testing methods, such as X-ray inspection, automated optical inspection (AOI), and boundary scan testing. These methods can help to detect solder joint defects and ensure that the PCB meets the necessary performance and reliability requirements.
Frequently Asked Questions (FAQ)
- What is the typical pitch of a Micro BGA package?
-
The typical pitch of a Micro BGA package ranges from 0.3mm to 0.5mm.
-
What are the advantages of using a Micro BGA package?
-
Micro BGA packages offer several advantages, including high-density interconnections, improved electrical performance, enhanced thermal performance, and space savings.
-
What are the challenges of using a Micro BGA package?
-
Micro BGA packages present several challenges, including tight tolerances, soldering difficulties, inspection challenges, and thermal management.
-
What factors can affect Micro BGA tolerance?
-
Several factors can affect Micro BGA tolerance, including pad size and shape, solder mask opening, via placement, and PCB fabrication tolerances.
-
What are some best practices for designing PCBs with Micro BGA packages?
- Some best practices for designing PCBs with Micro BGA packages include using appropriate pad sizes and shapes, using appropriate solder mask openings, minimizing via placement near Micro BGA pads, using appropriate PCB fabrication tolerances, and using appropriate soldering techniques.
Conclusion
Micro BGA packages offer several advantages for modern electronic devices, including high-density interconnections, improved electrical performance, and space savings. However, the small size and fine pitch of Micro BGA packages also present challenges in terms of PCB design and manufacturing tolerances.
To ensure optimal performance and reliability, it is important to consider several factors when designing and manufacturing PCBs with Micro BGA packages, including pad size and shape, solder mask opening, via placement, and PCB fabrication tolerances. Additionally, appropriate soldering techniques and manufacturing processes, such as solder paste printing, component placement, and reflow soldering, are critical for achieving reliable solder joints and minimizing the risk of solder joint defects.
By following best practices for PCB design and manufacturing, and by working closely with PCB fabricators and assembly providers, designers and engineers can successfully implement Micro BGA packages in their electronic devices and achieve the necessary performance and reliability requirements.
0 Comments